Wade Aitken-Palmer, of Kansas City, Mo., is among the 35 Michigan Technological University Master’s International students currently combining Peace Corps service with a graduate degree. He has been serving as a science teacher volunteer in Ghana since June 2012 and is pursuing a master’s degree in Mechanical Engineering from MTU
Nanosatellites are smartphone-sized spacecraft that can perform simple, yet valuable, space missions. Dozens of these little vehicles are now tirelessly orbiting the earth performing valuable functions for NASA, the Department of Defense and even private companies.
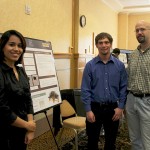
The Sustainable Futures Institute is again hosting seven middle and high school teachers from Michigan and Wisconsin in a six-week research experience for teachers (RET) program funded by the National Science Foundation. The teachers are conducting state-of-the-art biofuels research projects in engineering and forestry in the labs of Shehkar Joshi (SFRES/Bio Sci), David Shonnard (Chem Engg), and Jeffrey Naber (MEEM).
MTEC SmartZone is celebrating a 10-year milestone. From humble beginnings, the high-tech business incubator transformed the cities of Houghton and Hancock into a vibrant and growing technology sector, creating more than 350 jobs locally.
If you are looking for “mechanical engineering programs that stand out from the pack,” the MechanicSchools.com website lists Michigan Tech as one of the top five schools to consider.
Find out more
His cell phone area code is still 906, reflecting his Upper Peninsula roots, but Rob Waara’s role as chief engine engineer with the SRT Viper racing team has taken him far afield, including to the 24 Hours of Le Mans.
The Center for Diversity and Inclusion sponsored this year’s MiCUP/MI-LSAMP Research Gallery Walk, held on Thursday, June 20, in the Rozsa Center Lobby.
The event recognizes the research of students participating in the seven-week Michigan College/University Partnership Program (MiCUP) and the Michigan Louis Stokes Alliance for Minority Participation (MI-LSAMP) Program here at Michigan Tech.
Michigan Tech is partnered with MI-LSAMP to continue our shared goal of increasing the number of underrepresented minority and first-generation students in STEM and non-STEM fields.
Taking another step toward making affordable and durable prosthetics available to India’s low-income population, a team of Michigan Tech senior design students have redesigned and cost-optimized a prosthetic knee.
MORE
What’s a university education worth? That’s a question often asked by students, parents and legislators.
According to 2013 rankings recently released by PayScale, Michigan Technological University’s graduates rank 18th in the nation among 437 public universities in the return on investment (ROI) from their degrees. PayScale compares the cost of a college education to the salaries earned by graduates.