Open-source 3D printed parts often stronger than proprietary versions
A common criticism of home 3D printers is that whilst they can easily replicate any number of shapes and objects, and print parts that look identical to plastic prints from professional 3D printers, they can only print flimsy plastic trinkets. Are RepRap prints as strong as professional 3D printed parts using the same polymers?
“We were curious too. Our prints seemed strong, but we wanted to engineer robust scientific equipment and tools for the developing world, so we needed solid trustworthy numbers.” said Joshua Pearce, an associate professor of Materials Science & Engineering and Electrical & Computer Engineering and Michigan Technological University.
Read more at www.3ders.org
Michigan Tech Study Suggests Some RepRap 3D Prints Are As Strong as Commercial 3D Printers
If you thought that plastic parts produced from your average RepRap desktop 3D printer were in any way weaker than those made with commercial 3D printers, you may be proven wrong. The research lab of Dr. Joshua Pearce at Michigan Technological University has once again put out a study in favour of low-cost 3D printing. After already establishing that such devices could create affordable open source lab equipment for universities, as well as save consumers $300 to $2,000 a year with the printing of common household items, Pearce’s lab has tried to demonstrate that low-cost 3D printers can print ABS and PLA parts with the same strength as those made with commercial printers.
Read more at 3D Printing Industry.
In Print
Joshua Pearce (MSE/ECE) co-authored a paper “Photovoltaic system performance enhancement with non-tracking planar concentrators: Experimental results and BDRF based modelling,” published by the IEEE.
Graduate student Brennan Tymrak (ME), alumna Megan Kreiger (MSE) and Pearce (MSE/ECE) published Mechanical properties of components fabricated with open-source 3-D printers under realistic environmental conditions in the journal Materials and Design.
Pearce (MSE/ECE) also published Open source 3D printing allows you to print your own cheaper health devices in Conversation.
From Tech Today.
In the News
Joshua Pearce (MSE/ECE) was interviewed in the Forbes/Wolfe Emerging Tech Report, Feb 2014 on Modeling and Open Source World for 3D Printing.
From Tech Today.
On the Road
Joshua Pearce (MSE/ECE) presented an invited talk on Open Source 3D Printing at Stacking Layers: A symposium on 3D printing technologies and applications in Tallahassee, Florida, recently.
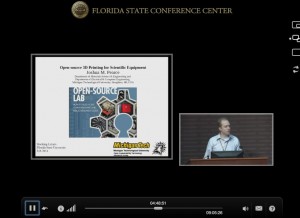
From Tech Today.
3D printing with metal at Michigan Technological University
3D printing has become a useful tool, but so far has been limited in the materials it can use. Michigan Tech researchers are now developing a way to print 3D objects using metal.
View the YouTube Video, by Michigan Tech.
In the News
Research completed by graduate student Brennan Tymrak (ME), alumna Megan Kreiger (MSE) and Pearce (MSE/ECE) was highlighted by 3D Printing Industry in“Michigan Tech Study Suggests Some RepRap 3D Prints Are As Strong as Commercial 3D Printers.”
The life cycle analysis research of distributed recycling by alumnae Megan Kreiger (MSE) and Meredith Mulder (MSE), current MSE student Allie Glover, and Pearce (MSE/ECE) was covered extensively by the media including CNN/Money, Yahoo News and Ars Technica.
From Tech Today.
Michigan Tech Study Suggests Some RepRap 3D Prints Are As Strong as Commercial 3D Printers
If you thought that plastic parts produced from your average RepRap desktop 3D printer were in any way weaker than those made with commercial 3D printers, you may be proven wrong. The research lab of Dr. Joshua Pearce at Michigan Technological University has once again put out a study in favour of low-cost 3D printing.
There’s still a great deal of research ahead of the team, to further elucidate the properties of objects printed with low-cost 3D printers, such as the effects of chemical post-processing on the strength of a print. Pearce explains, “This study only looked at the tensile strength in the plane of the print bed, next we need to expand this study to look at interlayer adhesion.”
Read more at 3D Printing Industry, by Michael Molitch-Hou.
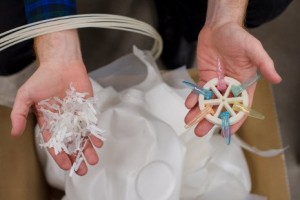
In the News
CBS Detroit and its Technology Report published an article about Associate Professor Joshua Pearce’s (MSE) work using recycled milk jugs for 3D printing material. See CBS Detroit.
From Tech Today.
In the News
Research completed by graduate student Brennan Tymrak (ME), alumna Megan Kreiger (MSE) and Joshua Pearce (MSE/ECE) was highlighted in the EE Times article“Measuring Open Source Hardware 3D-Printed Material Strength.”
***
Pearce was also interviewed about how 3D printing is environmentally green on Living on Earth–PRI’s Environmental News Magazine.
***
Professor Paul Sanders (MSE) and Pearce were interviewed on ABC10.
From Tech Today.
3-D Printing is Green
CURWOOD: Back before the industrial revolution, if you needed some thing, you or someone else would make it by hand. Then along came the production line and big machines that could mass produce items quickly and cheaply. And now we are headed back to future with so-called 3D printing, where a fairly small machine can make just about any metal or plastic object simply by following precise instructions from a computer. A team at Michigan Technological University has studied the possible environmental and the financial benefits of 3D printing. Joshua Pearce led the research and explains the surprising results.
Read the transcript or listen to the audio stream/download at Living on Earth, with Steve Curwood and Joshua Pearce.
Michigan Tech creates 3-D printer
“What our group has done hear at Michigan Tech is radically pushed the cost of 3-D printers down. So commercial 3-D printers that could do plastic used to cost $20,000. Now with the Open Source project, that cost has come under $1,000 and the ones we are building with our students cost under $500,” Materials Science and Engineering Associate Professor Dr. Joshua Pearce said.
Assistant Professor Paul Sanders said when he heard about 3-D printing with plastic, he questioned if it could be done with metal.
“This is essentially welding but it’s different because instead of joining two big pieces of metal, we’re making everything out of the weld wire itself,” he said.
Read more and watch the video at ABC 10, WBUP | WBKP.
In the News
Pearce was also interviewed by 3D Printing Industry in the article “3D Printing Plastic — Distributed Recycling and Distributing the Benefits.”
***
Michigan Tech’s 3D-printing program was highlighted in The Conversation article“Researchers can be ‘digital blacksmiths’ with 3D printers.”
America Makes – Michigan Tech Low Cost 3D Metal Printer
America Makes is the National Additive Manufacturing Innovation Institute. They focused on 3D metal printing initiatives at Michigan Tech in the new video “America Makes Moment.” Several people from Michigan Tech were interviewed, including President Glenn Mroz, Associate Professor Joshua Pearce, and Mark Bonefant, Instructor of CAD & Woodworking, Calumet High School. Featured were several students, instructors, and researchers, including Assistant Professor Paul Sanders.
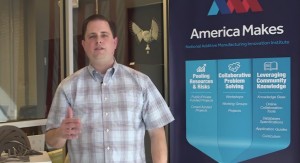
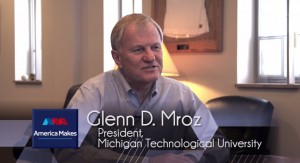
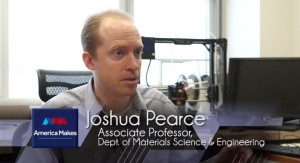
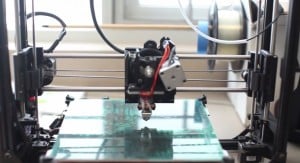
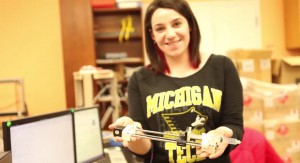
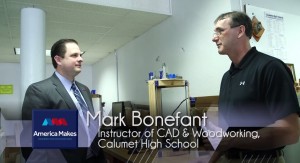
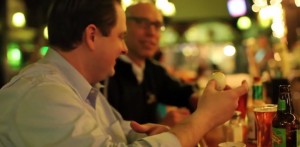