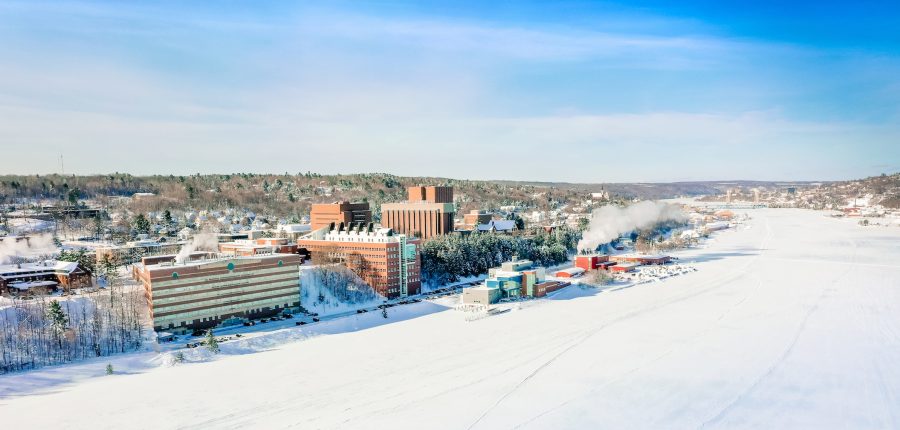
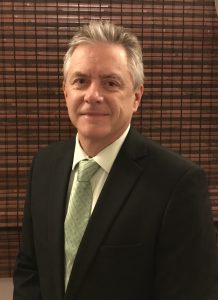
Dear Friends,
Even though it has been yet another pandemic year for us all, I want to share some good news. Despite all the challenges, we are still thriving here at Michigan Tech. We hope you are too.
This past week, 16 of our MET students graduated at Michigan Tech’s mid-year commencement, and most have accepted offers for engineering positions.
Our fall 2021 MET freshman class was again one of the larger groups in recent history at 24 students (same as last year). And our total enrollment for the MET degree program reached an all-time high: 172 students.
Several students enrolled in online courses to attain a graduate certificate in Manufacturing Engineering, which was initiated this year. The majority are MET alumni who work in manufacturing-related positions. In addition, we offer a new MS in Manufacturing Engineering and will soon begin accepting applicants for fall 2022.
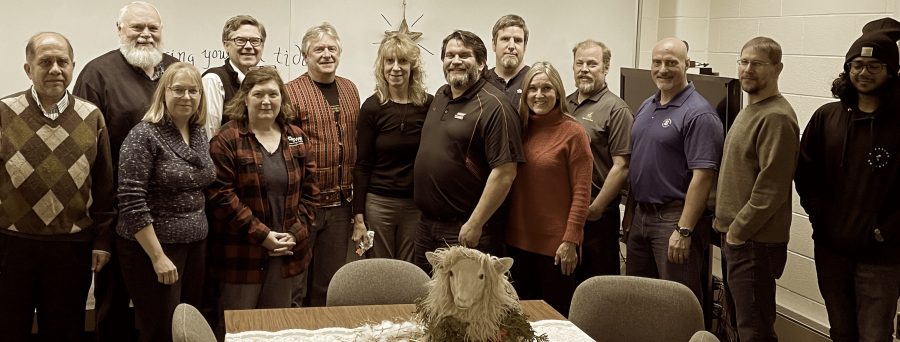
Here in MMET, we continue to support the very popular new interdisciplinary MS degree in Mechatronics, offering five graduate courses including an innovative new course, MET5400: Key Factors of Holistic Safety Programs.
We look forward to a productive new year for 2022. We will continue to strive to prepare hands-on professionals that can apply industry 4.0 methodology. Please visit MMET to see our newly developed Mission, Vision, and Goals.
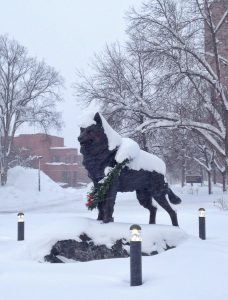
Be sure to reach out to me with any questions, and let me know if you have any news you would like to share. I always enjoy hearing from you.
On behalf of all of us in the Department of Manufacturing and Mechanical Engineering and Technology, I wish you all a very happy and healthy holiday season.
John Irwin, Professor and Chair
jlirwin@mtu.edu
Support MET: https://www.mtu.edu/mmet/department/giving/