I’ve just received an amazing gift. A unique, foundry-casting of my name in brass. The Michigan Technological University foundry is one of the few remaining operational university metallurgical facilities where students can work to create 3D positive prints, stamp them into sand, and then pour (with eye protection, fireproof aprons and face shields, tongs, and gloves) orange-hot molten metal into the sand to create metal castings.
I’m near the end of my first year as Dean of Engineering at Michigan Technological University. As background, it’s relevant to note that Michigan Tech was founded in 1885 to support the emerging copper and iron mining activities Michigan’s western Upper Peninsula. Founded to train the future mining and metallurgical engineers, Michigan Tech through the years has established an incredibly strong reputation for training “can-do” engineers—many who know a bit about metallurgy! But even I was surprised when presented with a personalized nameplate for my office—cast in the MSE foundry using brass recovered from a cache of old university office keys!
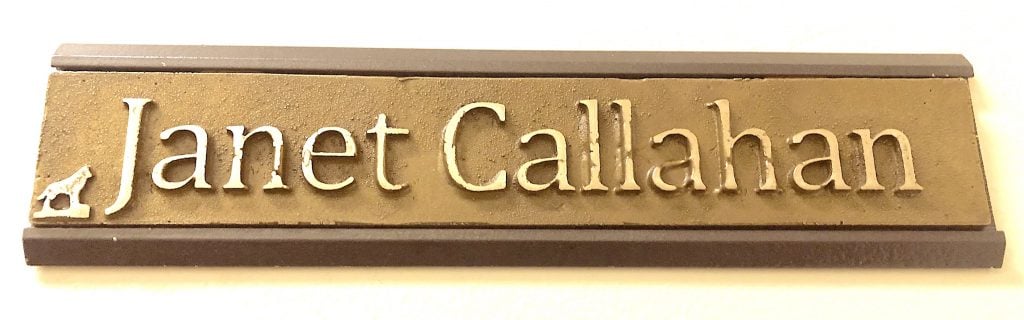
The university had accumulated a large number of brass keys from locks that were long-ago decommissioned. Looking for an ultimate way to securely dispose of the keys, the university public safety department approached the foundry team to ask if they could be melted and destroyed using the foundry. “Of course,” they replied. Timing is always important. At about that same time, Materials Science and Engineering Chair Steve Kampe had asked the foundry team to make a nameplate for me. I was just starting my new job as Dean, and happened to have my own credentials as a metallurgical engineer. Over the next several weeks, a pattern was 3D printed and the key brass was compositionally modified to facilitate its use as a casting alloy—and the nameplate came to be.
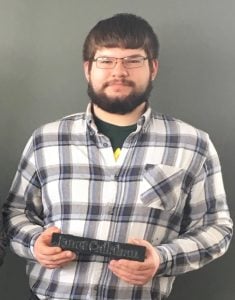
The “Dean nameplate project” was led by Sam Dlugoss, a chemical engineering student hired as a co-op employee in the foundry. I am humbled each time I see it as I unlock my office door with my own brass key. I think about the hands of the graduate students, staff, and faculty that are represented in the keys that ultimately were melted into my nameplate—and how these dedicated and aspiring engineers and scientists carried their keys and opened their labs and offices each day for many years, to do the work that has established the reputation we now carry on at Michigan Tech.
Last week, students in the foundry created more nameplates, this time for our College of Engineering Advisory Board Members. In the photos below, the students are working with iron.
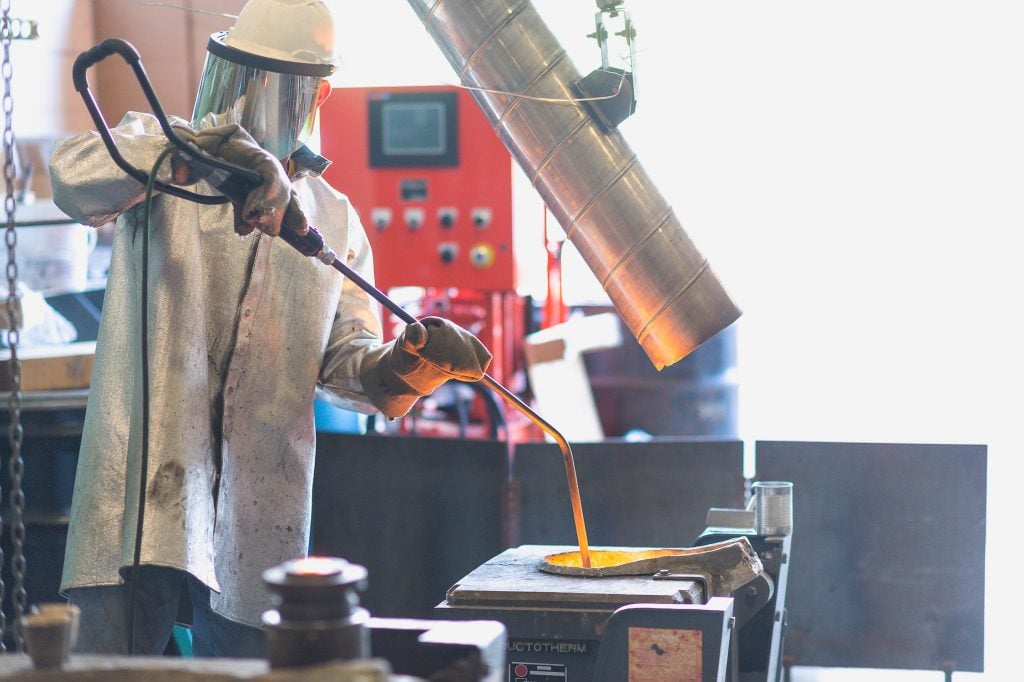
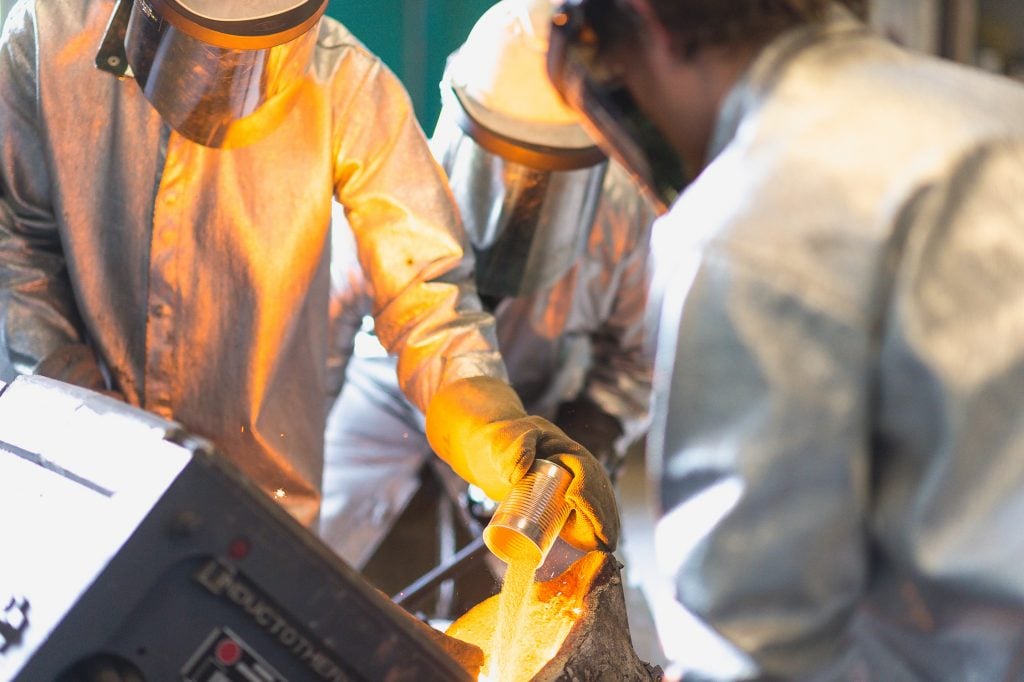
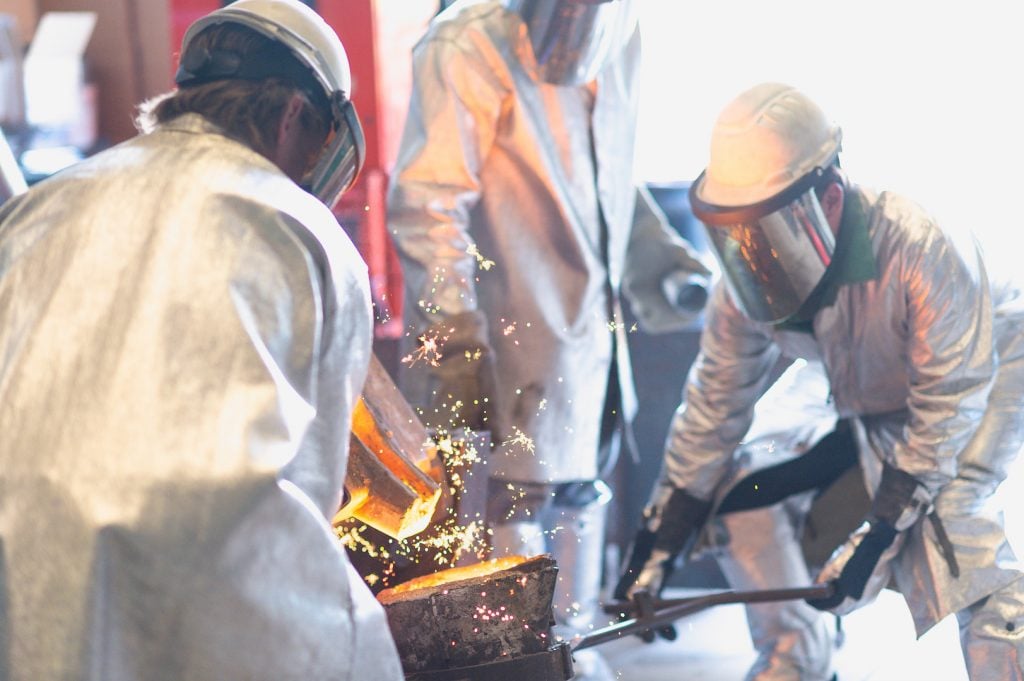
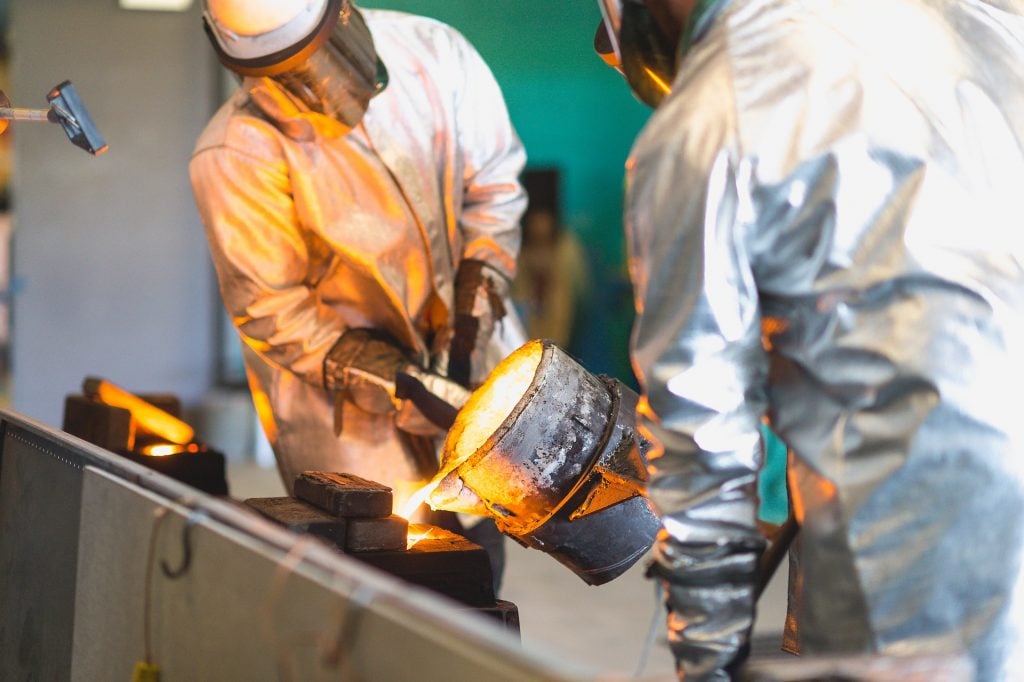
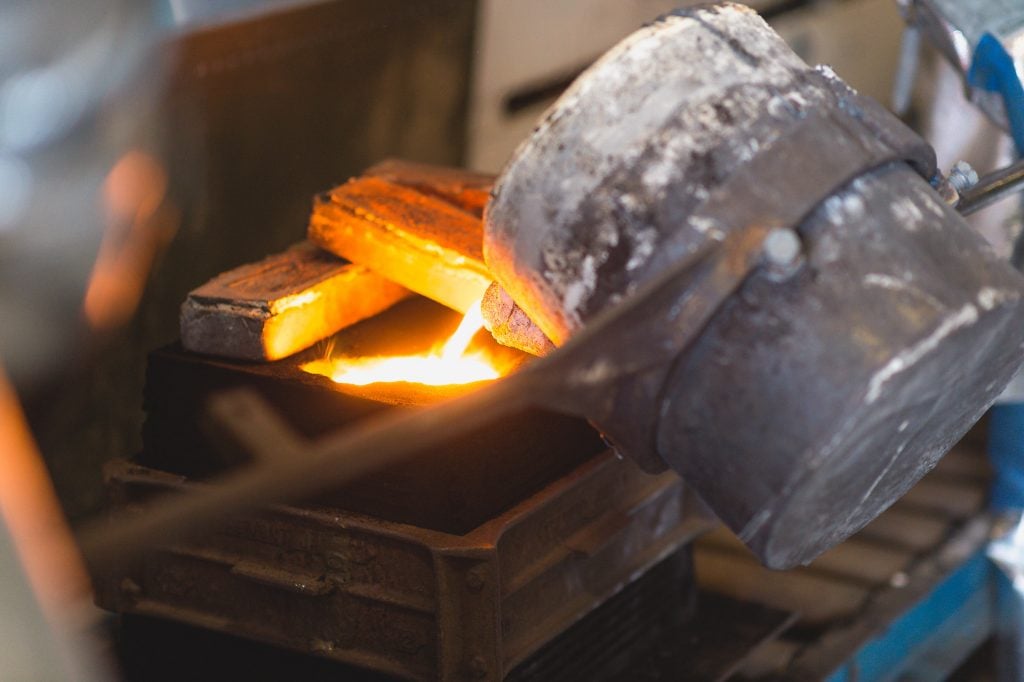
![As the pouring team fills the 3rd mold [middle ground], an MSE staff member [foreground] lifts the mold jacket from the 2nd mold, and will transfer it to the waiting 4th mold [background] prior to it being poured. The jacket supports the green sand mold against the hydraulic pressure of the liquid metal entering the mold.](https://blogs.mtu.edu/engineering/files/2019/06/Michigan-Tech-foundry-as-pouring-team-fills-3rd-mold-682x1024.jpg)
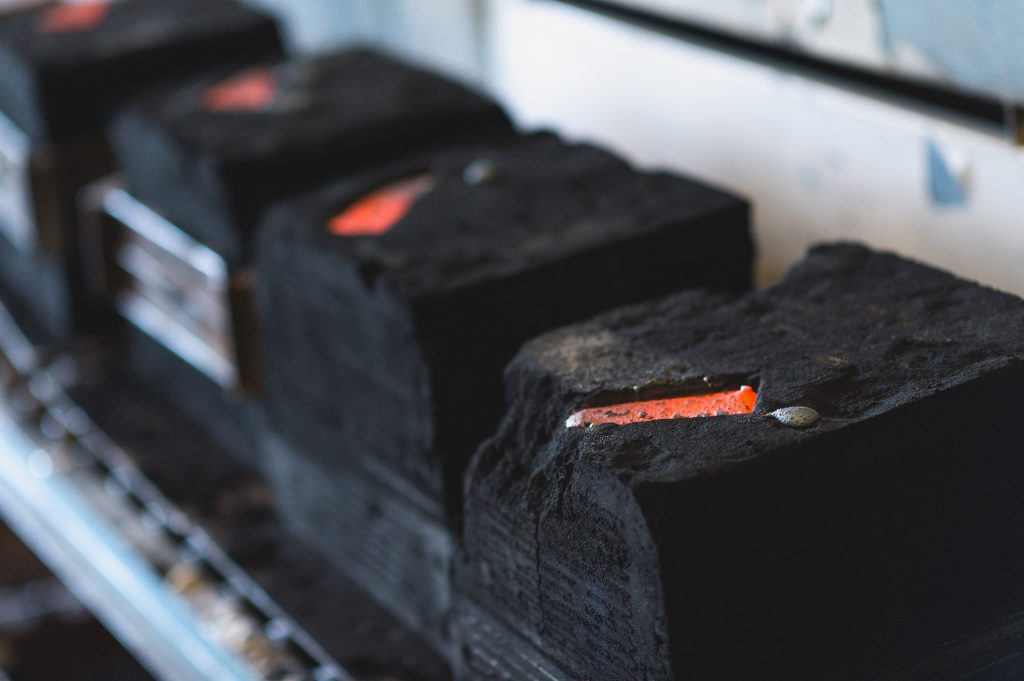
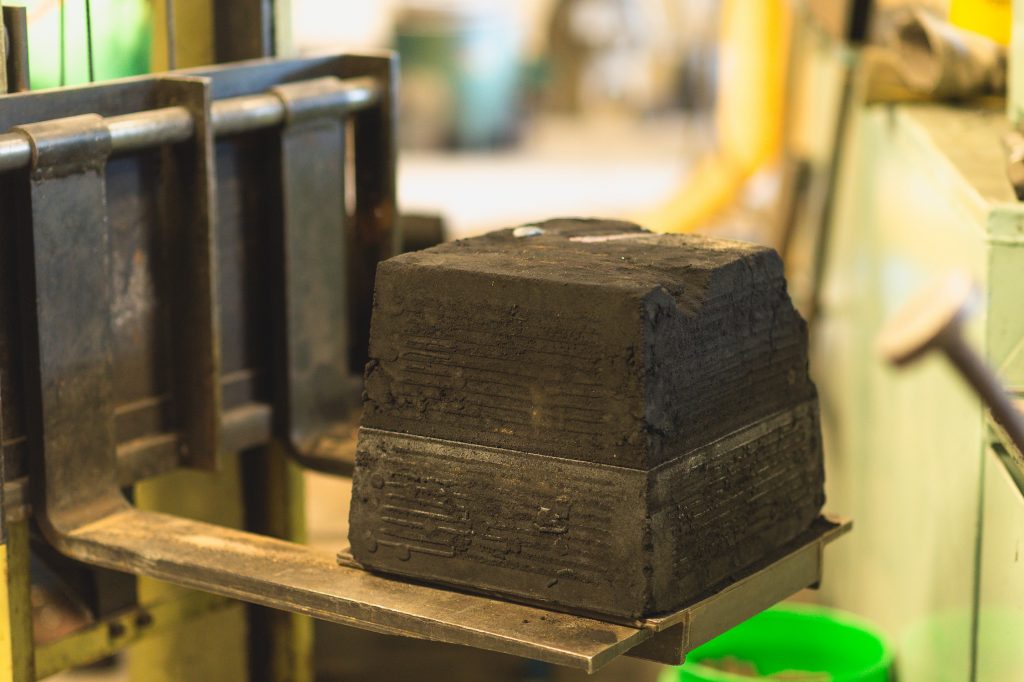
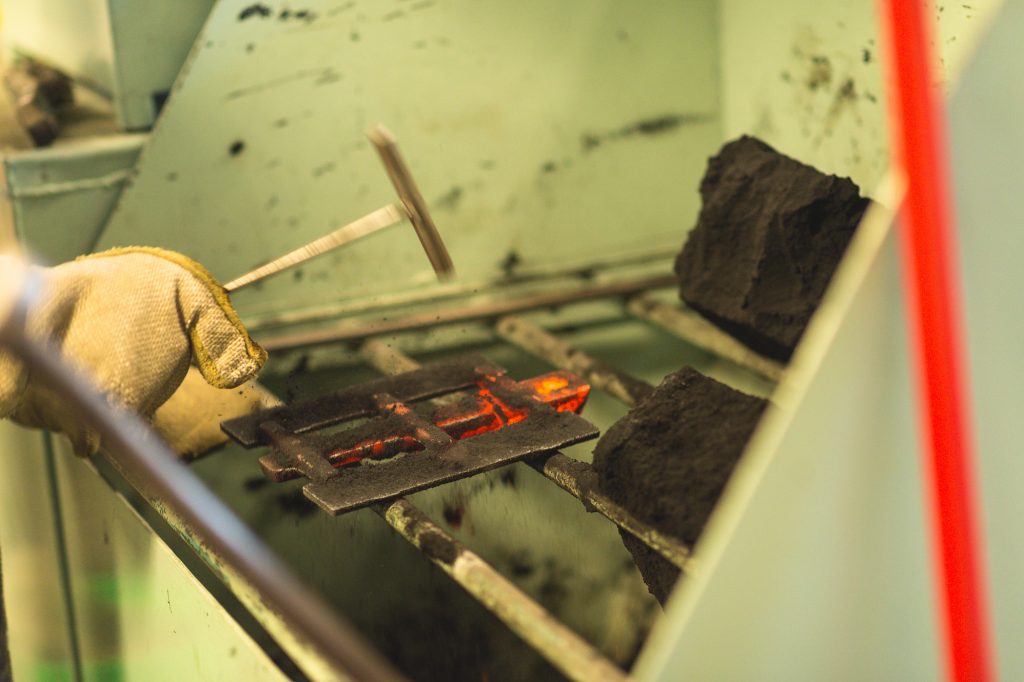
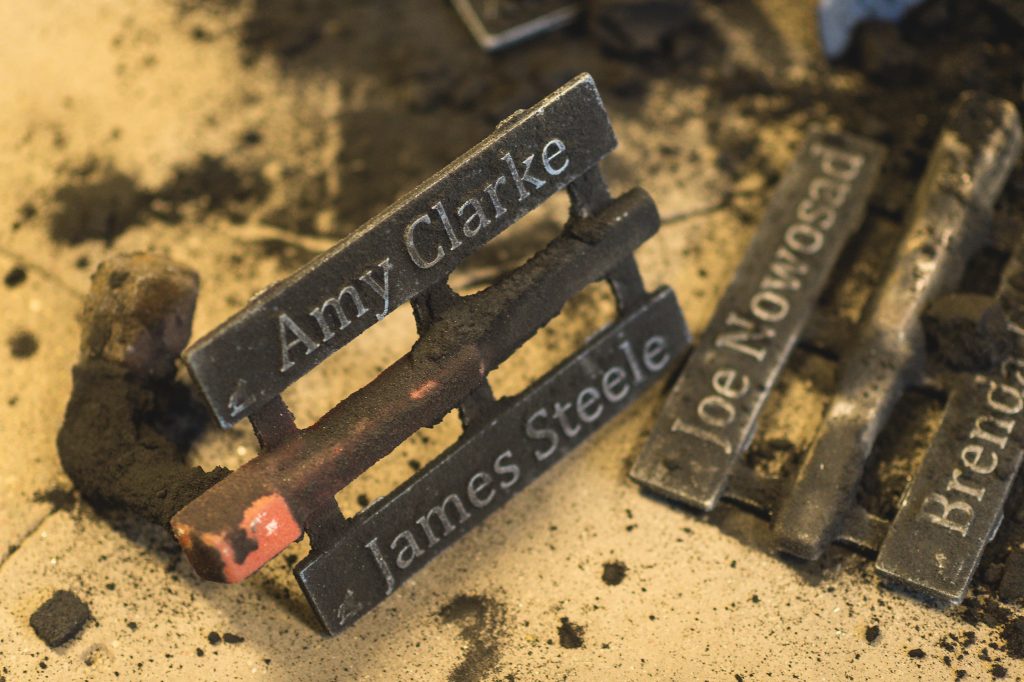
Now, if you’re interested in metallurgy, and you want to know more, please let me know—Callahan@mtu.edu.
Janet Callahan, Dean
College of Engineering
Michigan Tech