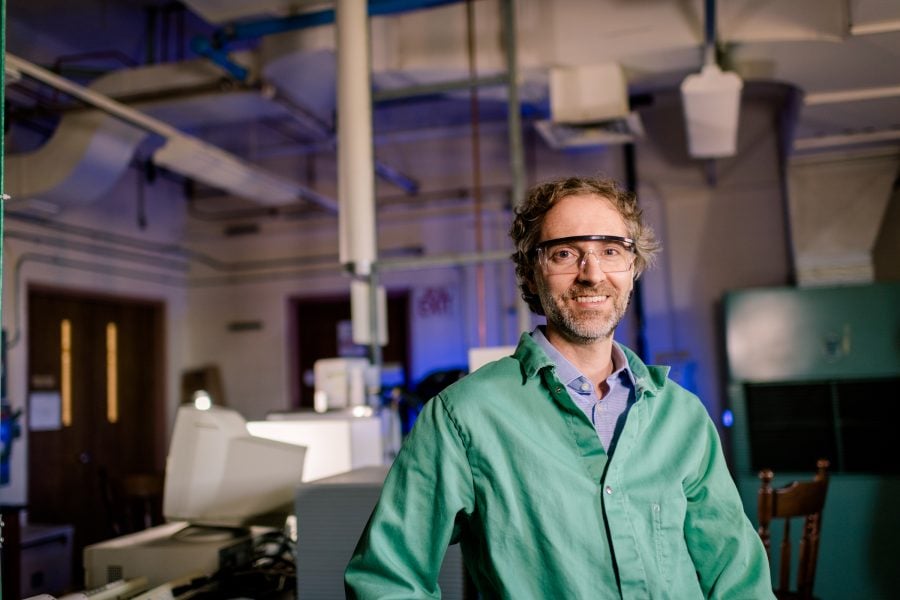
Leading the charge in developing a new lighter, stronger, tougher polymer composite for human deep space exploration, the Ultra-Strong Composites by Computational Design (US-COMP) institute under the direction of Dr. Greg Odegard has pivoted with agility during their final year of a five-year project.
The NASA-funded research project brings together academia and industry partners with a range of expertise in molecular modeling,manufacturing, material synthesis, and testing.
“When we began developing these ultra-strong composites, we weren’t sure of the best starting fibers and polymers, but over time we started to realize certain nanotubes and resins consistently outperformed others,” says Odegard. “Through this period of development, we realized what our critical path to maximize performance would be, and decided to focus only on that, rather than explore the full range of possibilities.”
US-COMP PARTNERS
- Florida A&M University
- Florida State University
- Georgia Institute of Technology
- Massachusetts Institute of Technology
- Pennsylvania State University
- University of Colorado
- University of Minnesota
- University of Utah
- Virginia Commonwealth University
- Nanocomp Technologies
- Solvay
- US Air Force Research Lab
For the past 21 years, scientists around the world have invested time, money, and effort to understand carbon nanotubes. But the islands of knowledge remain isolated in a vast sea of unknown behavior.
“When we started the project, we were confident we were going to put effort into getting the polymers to work well. The last thing we expected was the need to focus so much on the carbon nanotubes—but we’re putting effort there, too, using modeling and experimental methods,” Odegard notes.
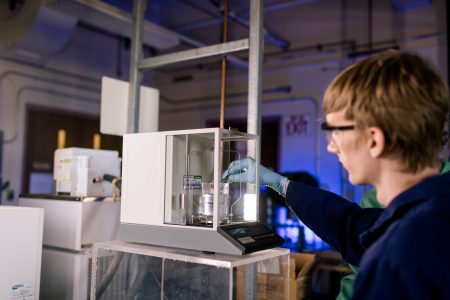
The challenge when working with carbon nanotubes is their structure. “Under the most powerful optical microscope you see a certain structure, but when you look under an SEM microscope you see a completely different structure,” Odegard explains. “In order to understand how to build the best composite panel, we have to understand everything at each length scale.”
The US COMP Institute has created dedicated experiments and computational models for the chosen carbon nanotube material at each length scale. “We can all see the different parts in our sub-groups and then we communicate that to the rest of the team, building a more complete picture from the little pictures at the individual scales,” he says. “We found the hierarchical modeling approach is hard to make work and what works best is a concurrent approach. We each answer questions at our own length scales, feed our findings to manufacturing, and then see how they in turn tweak the processing parameters.”
“We’ve achieved a remarkable workflow and a new model for collaboration.”
Achieving their Year Four goal to understand the internal structure of the carbon nanotube material, the institute has shifted focus to surface behaviors. As part of the project, they are tasked with bringing the carbon nanotube material together with the final selected polymer.
“We are looking at the surface treatment and how to get it to best work with the polymer of choice. We are excited to expand our scope of machine learning methods to better understand the carbon nanotube material. This accelerates our understanding of how processing parameters impact the structure, and how that ultimately impacts the bulk material properties.”
While machine learning has been part of the project scope from the beginning, the computational team is using their collected data to build a series of training sets. “The training sets will allow us to perfect our algorithms, learn from them, and hopefully influence product performance—potentially illuminating patterns we didn’t even see,” Odegard explains.
As the project draws to a close this year, the team continues to analyze their objectives set by NASA, which focus on producing a material that offers triple the strength and stiffness of the current state-of-the-art. As Odegard puts it, “The objectives set on this project are difficult to achieve. We knew that when we started. Regardless of whether we meet the numbers, as a group we have been able to push the envelope way beyond where we started in 2017—expanding the performance in a very short time period. This was made possible through remarkable collaboration across the institute.”