Last week, I was fortunate to be granted the opportunity to participate in an improvement event at ThedaCare in Appleton, Wisconsin. I was a “fresh eyes” participant on a team that was looking to make improvements in the outpatient lab scheduling process at ThedaCare hospitals. As someone who has interests in both healthcare and Lean, participating in this event was a fantastic opportunity to see firsthand how the two work together.
The biggest “a-ha!” moment I had during my week at ThedaCare was the use of a SIPOC Process Map. I only had a vague understanding of what SIPOC was and did not really know the value or purpose of the tool prior to this event. The SIPOC map, in addition to showing the suppliers, inputs, process, outputs, and customers, identifies the “trigger” for the process to start and the signal that the process is complete.
A SIPOC map can be used to provide a high-level overview of the process and define the scope. The well-defined “trigger” and “done” signals in a SIPOC map help prevent “scope creep” from occurring. “Scope creep,” is when the team widens their improvement discussion beyond the goals of the project. In the ThedaCare kaizen event, any issues the team identified that were outside of the scope (not on the SIPOC diagram) were put into an Out of Scope Parking Lot for future referral. This allowed the team to focus on our scope, but ensured that the other ideas for future improvements wouldn’t be lost.
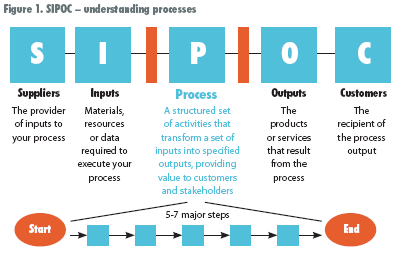