Last week I was involved in a kaizen event that was organized to counteract problems within the ordering and distribution of caps and gowns for graduation. Issues the team worked through were the logistics of the sporadic influx of inventory (40-60 large boxes that flood the inventory space twice per year) and the long lines customers dread to obtain their cap and gown. One important concept I learned from this kaizen was the importance of going to the gemba. To fully understand the issues and problems, we found ourselves taking many trips to the gemba – the place where the work happens.
As noted by Wikipedia, problems are visible at the gemba, and the best improvement ideas will come from going to the gemba. For this kaizen, we spent some time in the inventory room of the Michigan Tech Campus Bookstore to take a look at the current situation. The picture below shows discussion during one of our gemba visits (note the large boxes that don’t even fit on the shelf). Each time we went to the inventory room we were better able to understand the limitations of the space and brainstorm countermeasures.
“Gemba walks” are not just for kaizen events. Ideally they should be done as often as possible to provide supervisors and management with a true picture of what workers are experiencing on a day-to-day basis. Mark Graban, a lean consultant with a focus on healthcare, recently wrote about an article by Delos Cosgrove, President and CEO of Cleveland Clinic, and his experience with going to the gemba. These walks are not only important in industries or businesses with physical inventory such as manufacturing, merchandising, or healthcare. In a knowledge-based industry it is still effective to go to the place where work is being done on a regular (though unscheduled) basis to “go see, ask why, [and] show respect.”
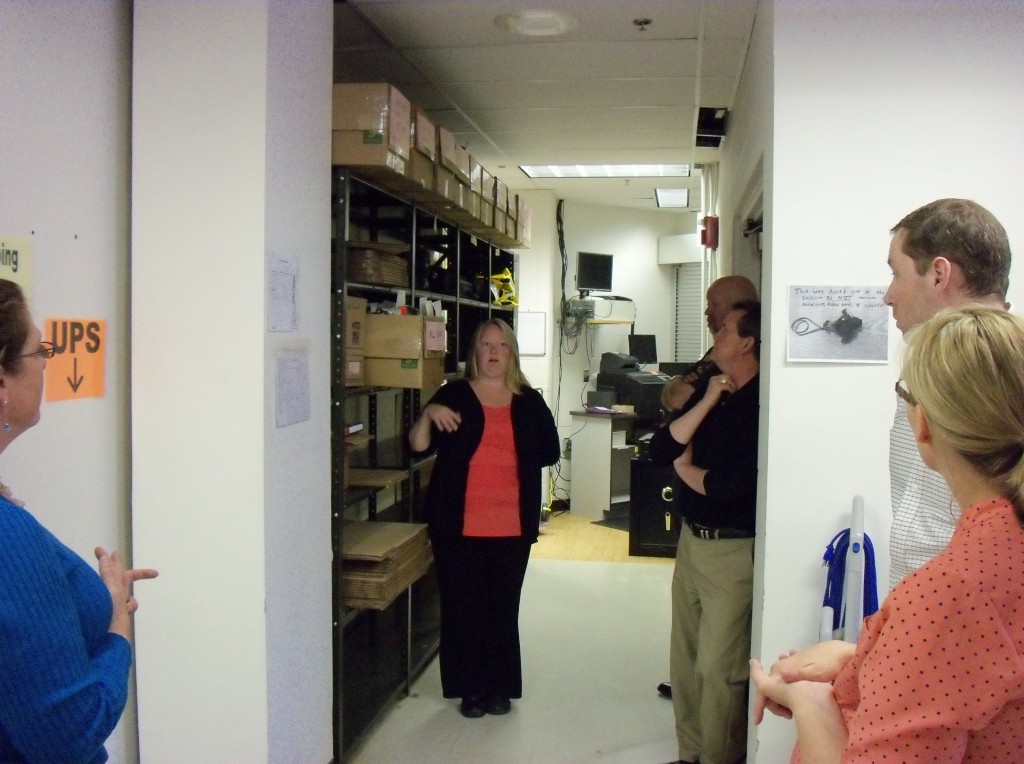