Why an overview? Sometimes after you’ve been doing something for a while, it’s easy to forget the basics. For example, if you play the piano and you never practice your scales, you might forget them or get a little rusty. Lean isn’t any different! Sometimes it’s good have a refresher on what it’s all really about, so that’s why this week I’ve decided to do a brief Lean overview.
First off, what is Lean? Lean is a continuous improvement philosophy. It’s based upon respect for people, customer focus, and having stakeholders at all levels be involved in the improvements—especially the frontline workers who “live” in that process every day! Lean practice focuses on identifying and eliminating waste to improve value from the customer’s perspective.
Some key concepts of Lean are:
- Value is defined by the customer
- Identify the value stream for each product
- Create flow in your process
- Pull from the customer, and
- Continual pursuit of perfection.
What’s the value stream? All Lean thinking begins with a value stream! It includes all steps and activities in a process, from beginning to end. Value streams can be used to identify wastes (non-value added steps) to identify areas for improvement.
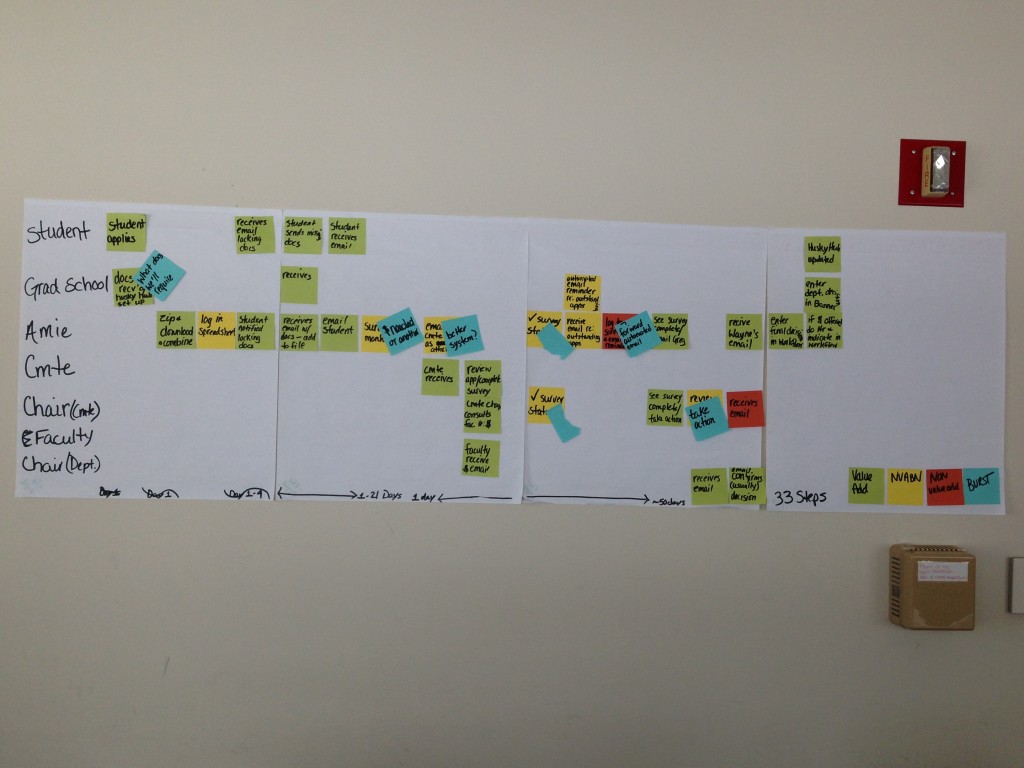
What’s the difference between value added and non-value added steps in a process? The value should always be looked at from a customer’s point of view, so a value-add step in the process is quite simply something your customer finds valuable, or something that they are willing to pay for. If it is a non-value added activity, it means your customer doesn’t see that step as a valuable part of the process. A non-value added activity is considered waste.
Some steps in a process may be non-value add, but necessary. These steps might be required by legislation, might be a quality check, etc. It is not a step that the customer necessarily views as valuable and feels they should pay for, but it is something that must be done regardless.
How do we define waste? Waste is anything that does not add value in the customer’s eyes. There are three forms of waste: unevenness (variation or inconsistency in a process), overburden (excessive stress or strain on people/equipment), and non-value added waste (see our Waste Quick Point in the Tools & Templates section for more info on waste).