Are you always searching for lost files or tools? Do items from your area seem to just “go missing”? Is it hard to find files on your shared network drive?
If you answered yes to any of these questions, the 5S Blitz might be for you! The 5S Blitz is a Lean Workshop for those who are interested in learning more about Lean and in using 5S to improve their (physical or virtual) work spaces. 5S can be applied to your personal desk, a lab, a supply area, a network drive, and more! The workshop will be taking place on January 28, 2014.
In the 5S Blitz, participants will have a learning session in the morning, and then will be able to go to their work space to start implementing 5S with the help of a campus Lean facilitator before coming back in the afternoon to share their progress and any lessons learned. Throughout the following two weeks, participants can continue to work on their 5S project before sharing their experience in an open report out.
If you’re interested in participating, you can find out more and register today on the Lean Workshops page of our website. You can participate individually or with others from your work area. All you need to register is a 5S project idea!
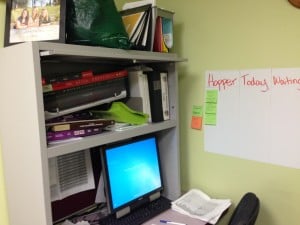
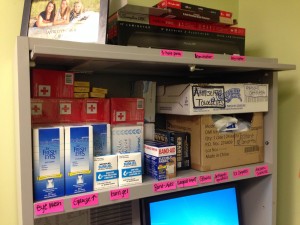