On Tuesday, March 11th, the Office of Continuous Improvement participated in the Customer Appreciation Fair held by Auxiliary Services in the MUB Ballroom. This event was held as a small token of thanks to all of Auxiliary Services’ customers for their patronage this past year. There were lots of fun games, good prizes, and great food. It was a great opportunity to get out of the office for a few hours and enjoy an afternoon of fun!
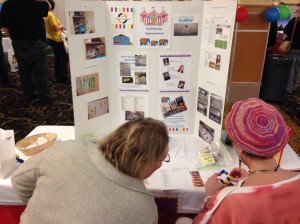
At the OCI booth, we decided to incorporate lean tools and lean thinking into our game: Standardized Work LEGO Man Building. One participant was given verbal instructions on how to build the LEGO man while the other was given written and visual instructions. Every time, the participant who was given the written and visual instructions finished building first. This was a fun exercise to show how beneficial standardized work and standardized job element sheets are in making processes more efficient.