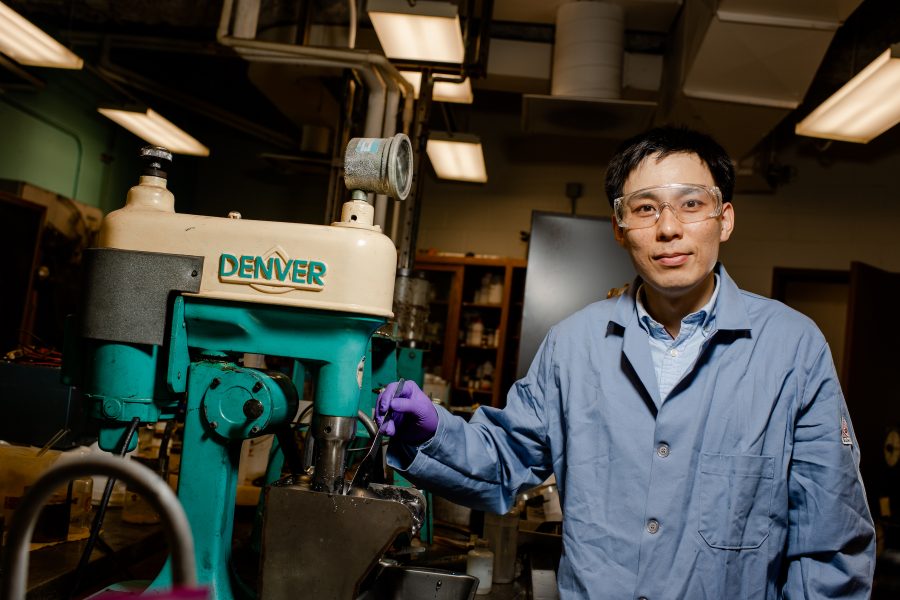
On Nov. 16, the Biden Administration announced a $74 million funding package to advance domestic battery recycling and reuse that will strengthen the nation’s battery supply chain. Michigan Technological University and Eagle Mine are co-recipients of part of this funding. $8.1 million will be used to prove new research technologies that develop sustainable processes to supply critical minerals for electric vehicle (EV) battery manufacturing.
An additional $2.5 million from the U.S. Department of Energy’s Advanced Research Project Agency-Energy grant program was also awarded to Michigan Tech and Eagle Mine, which will enable the University to study carbon dioxide mineralization opportunities in Eagle Mine’s tailings facility. The money will be used to develop new technologies that enable accelerated carbon mineralization using mine tailing minerals.
“Eagle Mine is proud to partner with Michigan Tech and support sustainable technologies that will create critical mineral pathways for future demand,” said Darby Stacey, managing director of Eagle Mine. “Eagle Mine is the only nickel mine in the United States, and the availability of our experience and use of our resources, waste streams and nickel concentrates are essential to understanding the societal impact of the nation’s transportation needs.”
“The state of Michigan is the home to the automotive industry, nickel mining industry and future lithium-ion battery industry in this nation,” said Lei Pan, associate professor of chemical engineering at Michigan Tech and principal investigator of both funded projects. “Addressing both the supply of critical minerals and reprocessing and reuse of mine tailings is critical to advance sustainability in the mining industry.”
MTEC SmartZone of Houghton and the Michigan Small Business Development Center contributed toward the successful grant application. In collaboration with Michigan Tech, MTEC leveraged the Michigan Economic Development Corporation’s Federal Match Program and Technology Transfer Talent Network program by providing matching funds toward cost-shares required in the $8.1 million award, and to recruit and hire an entrepreneur-in-residence for the project.
MTEC was also intimately involved in helping establish Nion Metals LLC and worked in concert with Nion Metals in the development of pro forma budgets, market analysis, competitor due diligence and technology commercialization planning. In addition, MTEC provided assistance with the grant writing, editing and review; developed presentation materials; and assisted in obtaining letters of support from industry and two national labs.
“This was a collaborative effort between Nion Metals, Michigan Tech’s Office of Innovation and Commercialization, MTEC SmartZone and Eagle Mine,” said David Rowe, CEO of MTEC SmartZone. “MTEC SmartZone’s mission is to accelerate high-tech business growth, and this project is a prime example of that function.”
“This robust investment will support Michigan Tech’s researchers, faculty and students’ continued efforts to develop and deploy the next generation of technologies to recycle electric vehicle batteries that will guide the future of the auto industry in Michigan and nationwide,” said Rick Koubek, president of Michigan Tech. “We thank our industry partners and Eagle Mine for supporting this research that will lead to new critical mineral technologies.”
The funding for the project, named the Nion Project, will help MTU and Eagle Mine address several economic and technical challenges in the lithium-ion battery recycling industry, including 1) low payable metals, 2) difficulty in achieving specifications for battery-grade lithium from mixed secondary feedstock, and 3) high operational costs and environmental impact of current state-of-the-art recycling practices.
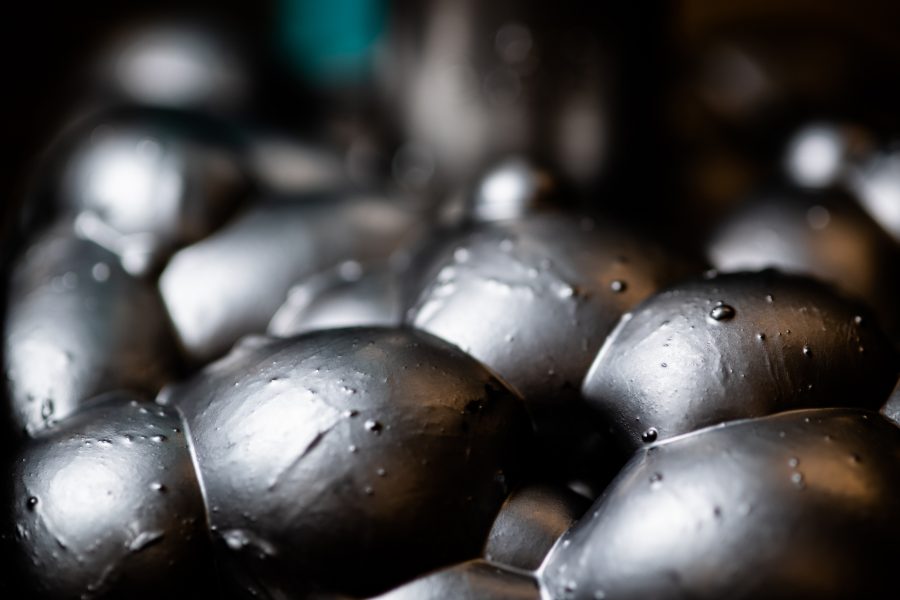
The funding will support the University in moving its research from the lab to a pilot-scale facility that will be newly constructed in the Upper Peninsula.
The project team consists of engineers and experts in subject matter, commercialization, permitting and investor/community engagement to ensure the success of this project, with the end goal of enabling the commercialization of these technologies to the benefit of the electric vehicle lithium-ion battery supply chain in the United States.
“We have the technology and resources in the Upper Peninsula to make a positive impact on the nation,” said Stacey. “This partnership will not only help advance new technologies in our nation but, if ultimately successful, will also bring new construction and jobs to the Upper Peninsula.”
Potential project impacts also include:
- Reducing total energy use and total greenhouse gas emission by at least 25% per nickel unit produced compared to the current state-of-the-art recycling practice.
- Establishing a profitable battery recycling business regardless of the types of cathode chemistry.
- Supplying additional nickel and cobalt minerals from unconventional resources. If further successful, an additional 56 million pounds of nickel and 2 million pounds of cobalt from Eagle’s Humboldt Tailing Disposal Facility could be recoverable.
About Eagle Mine
Eagle Mine is an underground, high-grade nickel and copper mine located in western Marquette County of Michigan’s Upper Peninsula. It is the first mine to be permitted under Michigan’s Part 632 Non-Ferrous Mineral Mining Law. The mine is expected to produce 440 million pounds of nickel, 429 million pounds of copper and trace amounts of other minerals over its estimated mine life (2014-2026).