At Wednesday’s (7/9) Lean Implementation Leaders and Lean Facilitators meeting, Bob Hiltunen (Director, Auxiliary Services) provided a wonderful teach back activity on the advantages of one-piece flow processing vs. batch-and-queue processing.
Background
One-Piece flow is one of the most important principles of lean manufacturing. One-piece flow means that parts are moved through operations from step-to-step with no work in process in between; either one piece at a time or a small batch at a time. Once work on a product begins it never stops moving until it is a finished product.
As opposed to one-piece flow, batch-and-queue processing is the action of producing more than one piece of an item and then moving those items forward to the next operation before they are all actually needed there. Batching and queuing tends to drive up inventory and lead time, and creates inefficiency in an operation. It also increases the space needed for production.
Teach back Activity
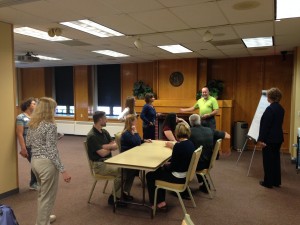
To complete this activity, 2 “directors,” 4 “managers,” 4 “workers, and 1 “customer” are needed. Each worker is a “station” at the table (as seen in the photo). The first three workers are assigned the task of flipping quarters and passing them to the next worker and this process repeats until the quarters reach the last worker who is asked to “stamp” them, and pass them to the customer.
The activity begins by simulating a batch-and-queue system with the first worker flipping all 30 quarters before passing them, in a batch, to the next worker and so on until they reach the customer. The batch sizes that are passed between workers are reduced after each subsequent round until each worker is flipping and passing only one coin at a time, to represent a one-piece flow system.
To measure the effect of the transition to one-piece flow, time measurements are taken at many times during the process:
- At the start of the process when the first coin is flipped
- When each worker first receives a coin from the previous worker
- When each worker flips and passes their last coin
- When the customer receives the first coin
- When the customer receives the last coin
As the activity progresses, the time each work station is active gradually increases, however, the time it takes for the coins to reach the customer dramatically decreases. In our simulation, the process time was reduced from 1 minute 30 seconds to 20 seconds.
The ideal state for a production process is continuous one-piece flow. If you can’t manage to get down to one-piece flow, always the question … can you get two-piece or three-piece? The most important thing to remember is the idea of continually moving closer to the ideal state.