Former Michigan Tech Lean consultant, Mike Taubitz, is featured in a podcast on Leanblog.org. Check it out HERE!
- Amanda Cadwell (Administrative Aide, Civil/Environmental Engineering & UAW President)
- Wendy Davis (Manager of Process Improvement)
- Bob Hiltunen (Director, Auxiliary Services)
- Ellen Horsch (Vice President for Administration)
- Rhonda McClellan (Facilities Helper, AFCSME member)
- Barb Ruotsala (retired, past UAW President).
A few Michigan Tech Lean Implementation Leaders/Facilitators will be traveling in the upcoming months for various Lean trainings. Stay tuned for updates regarding their training experiences:
Heidi Reid – “Toyota Kata” at University of Michigan
Wendy Jones – “Developing People with Capability for Lean” and “Coaching Skills for Lean Implementation Leaders” from Lean Enterprise Institute
Wendy Davis – “Lean Office Certificate” University of Wisconsin-Milwaukee
Training for these staff is supported by a grant from the Federal Mediation and Conciliation Service.
By Kaylee Betzinger, Student Process Improvement Coordinator
Lean Training funded by a grant from the Federal Mediation and Conciliation Service (FMCS) has been going on for the past several months. November 5th and 6th marked the last FMCS Lean Training sessions here on campus with our consultants, Mike Taubitz and Larry Osentoski. Two cohorts of employees completed Lean training:
- Lean Facilitators – trained to facilitate Kaizen Events for any campus department or area interested in making improvements.
- Lean Implementation Leaders – trained in Lean concepts aimed at building a Lean practice into the day-to-day work for an area or department.
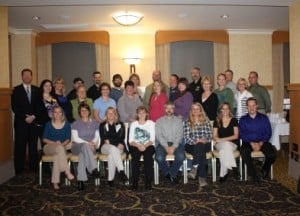
During the last training sessions each trainee participated in a Kaizen Event. The Lean Implementation Leaders chose a problem within their department for teams to work through and the Lean Facilitator teamed up to practice their Kaizen Event facilitation skills.
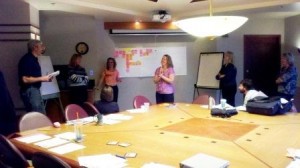
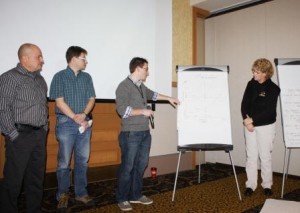
Each trainee had their own personal experience with the training. There were many laughs among the group and a lot of great memories. Some of the trainees share some of their experiences:
- Rachel Wussow: “When learning Lean tools and thinking Lean, I am challenging and improving myself as a professional. My customer is an 18 year old college student. So, I have to teach the Lean lessons to a different generation of thinkers. Lean is more than improvement it is sustaining and acting. The world is full of change and Lean is a tool of adjustment.”
- Cat Burns: “My first experience was very positive. I enjoyed working with people that I may not normally interact with. It felt great to officially start my involvement with Michigan Tech’s Lean Journey. I was lucky to have two great (and original) Facilitators work with me on my first Kaizen.”
Thank you to all our trainees, our consultants, and Manager of Process Improvement, Wendy Davis for making these training sessions so enjoyable and valuable!
Recently, Assistant Vice President for Administration, Theresa Coleman-Kaiser was interviewed for a Radio show on Michigan Business Network’s website . Theresa spoke about our Lean Journey and how Lean principles are becoming more widly practiced here at the University.
Click HERE to listen to her interview.
Lean Consultants, Larry & Mike, were on campus again this past week. During there visit, they facilitated a very memorable training exercise with our Lean facilitators. It involved each facilitator choosing a “Lean Tip” from a sheet of over 50 tips that Mike has collected throughout the years and relating that tip to their Lean training experience thus far. Here are some examples of the tips:
- Team members will become “lean thinkers” at different times; keep moving forward, sharing successes and lessons until you hit the tipping point for true culture change.
- Fairness and respect for all are cornerstones.
- Do not attempt changes/improvements without the input of affected stakeholders.
Kari Pietrzyk, Event Associate in the MUB presented on the tip, “the greatest risk is not taking one.” Here is her take:
“The greatest risk is not taking one. We would never learn if we never tried. We have to take risks to go further in our personal lives, like having children or starting a new job. Inventions would have never happened. There would be no airplanes, automobiles of computers. Life is full of risks, we need to choose wisely, to which ones will take us further and which ones will stop us in our tracks. We can learn from our mistakes or choose to ignore them. Every mistake is one step closer to doing something the correct way. I believe Lean is all about taking risks. To accomplish any task requires some risk. To make a process better also requires a risk.”
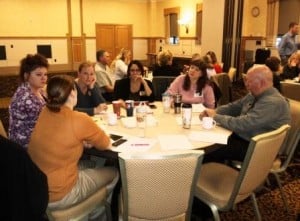
The third training session for Michigan Tech Lean Facilitators and Lean Implementation Leaders was held this week. These two training groups have four more sessions to complete the training. As a result of the training sessions, the participants will be expanding their training knowledge as they support future Lean improvements here at the University. If you are making improvements in your area or department, please contact me to have a facilitator help you out!
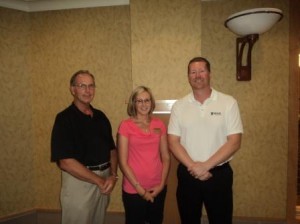
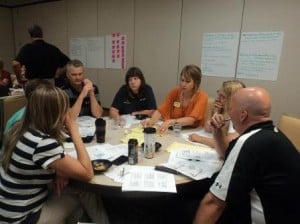
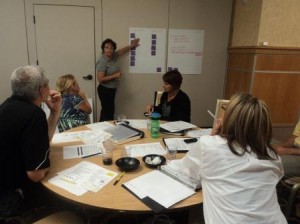
With grant funding from Federal Mediation and Conciliation Service, a team of two Lean professionals have been selected to provide Lean training on campus:
- Mike Taubitz is a retired General Motors manager. He has over 40 years of experience implementing Lean practice and culture. Mike currently serves as the Michigan Lean Consortium Secretary and is the principal of Lean Journey, LLC.
- Larry Osentoski is a Michigan Tech alumnus from Electrical Engineering. He is the owner of DRIVE Developments, Inc. and uses Lean concepts to shape his business practices.
The goal of this training and grant project is to build labor and management relations and communication using a Lean culture building model and approach to continuous improvement. Two groups of employees will be trained:
- Lean Facilitators – facilitate Lean improvement events
- Lean Implementation Leaders – lead a Lean transformation in their unit
There will also be opportunities for Lean learning available to all staff and faculty during consultant visits. Mike and Larry will be on campus about 2 days per month from May – November 2012. Please watch this blog and Tech Today for Lean training announcements!
Things have been heating up with the work for the grant project (goal: to expand the use of Lean Principles across campus, strengthen labor/mgmt relationships). The committee is developing two training programs that will be taught by an an external consultant. We will be looking for all levels of employees to apply for the training programs. Here are descriptions of them:
LEAN FACILITATORS
This cohort is designed to be half represented (union) employees and half non-represented employees. This group will develop a practiced understanding of what makes a Lean Organization, the Key Principles of Lean, and various tools and concepts. They will understand their role in improvement events, and will practice their skills by facilitating on-campus improvement events after the training.
LEAN IMPLEMENTATION LEADERS
This training is for non-represented staff that are positioned in their department or work areas to plan and implement a lean transformation. The training will give them a working knowledge to become a Lean practitioner and hands on experience applying Lean problem solving methods.
Stay tuned for details on a series of information sessions to learn more about these opportunities.
Things have been busy, October came and went in a blur. October was the first month of an 18 month grant cycle for a $55,006 grant received from the Federal Mediation and Conciliation Service Labor-Management Cooperation Grant Program.
The grant will support the Continuous Improvement Labor-Management Advisory Committee; an 11 member committee, composed of six “management” staff and five union staff (all three of Michigan Tech’s unions represented). The committee was put together to further develop the Continuous Improvement using Lean Principles Program as a method to improve labor-management relationships and increase staff participation in enhancing work environments.
Goals of this project include:
- Develop a Continuous Improvement/Lean Facilitators’ Training Program to train new facilitators and provide continued education to current facilitators.
- Recruit and train a cohort of 10-15 new campus facilitators, consisting of at least 50 percent unionized staff members.
- Develop an outreach and training program to introduce supervisors and management to the Lean model of continuous improvement and how it can enhance work processes and labor-management relations.
- Provide training to Michigan Tech employees who are key to managing and expanding the Lean continuous improvement programming developed as part of the Project.
- Sharing Michigan Tech’s model at a regional and national level via publications and presentations at key conferences, meetings, and workshops.
It is an exciting time period for Michigan Tech’s Lean Journey, the next 17 months will be busy yet rewarding.