It’s been nine years since China hosted the summer Olympics, nine years since the United States elected Barack Obama as the 44th President, nine years since the stock market crashed, and it’s been nine years since Michigan Technological University began it’s lean journey.
In 2008, University President Glen Mroz introduced Michigan Tech to Lean. In relative terms, nine years really isn’t that long, however, not a second was WASTED since the opening of our office, the Office of Continuous Improvement. After nine years, 236+ Kaizens (Improvement Events), 70+ Facilitators, 10 PICs, 2 Directors of Process Improvement, two classes, and one student organization, it is safe to say that our relationship with MTU’s campus is now BLOOMING.
We recently hosted our 2017 facilitator graduation ceremony and introduced 16 new facilitators to our pool! Congratulations to the new facilitators who are: Joan Becker, Debra Charlesworth PhD, Paul Charlesworth PhD, Johnny Diaz, Christina Fabian, Megan Goke, Timothy Griffin, Lori Hardyniec, Kristi Hauswirth, Brian Hutzler, Austin Kunkel, Lauren Movlai, Katherine Purchase, Joseph Snow, Madeline Mercado-Voelker, and Maryann Wilcox. These 16 people come from 13 different departments campus wide, and one has now left the university and is continuing their Lean journey in the community. These facilitators are another chapter of growth for this university and the mission is simple, to IMPROVE. It’s been said time and time again that probably the greatest aspect of Lean is the people and the culture. The culture is one of open-mindedness, collaboration, humility and respect. However, without the people, the culture would fail. We are proud to welcome this group of 16 to our culture.
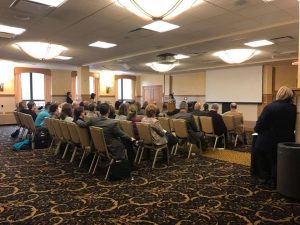
Our growth on campus has not only impacted the faculty and staff, it has also been growing within our student population as well. On the same day of graduation our office hosted it’s first ever Student Information Session. At this session our PICs taught students a little about what lean and continuous improvement is, along with an activity on personal kanbans. A few days after we hosted our information session, our student organization, Leaders in Continuous Improvement, received the award for the Most Improved Student Organization for the 2016-2017 academic year (how fitting).
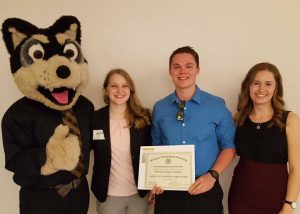
These three events all happened within the last week, highlighting the success lean is having at the university.
With our culture expanding and the amount of people involved rising, I know our university will soon be flourishing with Lean, and our students will be leaving here with skills that they not only learned in lecture and lab, but also from the environment that they are being surrounded by. This environment will provide everyone immersed in it with skills that companies, coworkers and employers are looking for such as team collaboration, problem solving, and again RESPECT for everyone. Lean and Continuous Improvement has proven over and over again that it is a way of life, a way of change, and a way of growth that anybody can take and adapt into their lives, and it has proven this to all that have hopped on board with our journey.
It’s been nine years since Michigan Technological University began it’s lean journey, and it is our DREAM that the blooming culture we have will flourish, and in nine years we’ll be able to look back on this time in our journey and have no words but “wow,” and no emotion but delight.