For the last six months a team has been pulled together to address various areas of the commencement process here at Michigan Tech, from ticketing to safety, and from configuration of space to guest speakers. This team has covered the commencement process inside and out, and with all of the stakeholders involved too! That’s HUGE!! The team has met 13 times already, for a total of 20 hours, and they are just getting started on most of it.
Before I introduce the teams let me tell a little bit more about how the Office of Continuous Improvement and the commencement committee have paired up and identified the kaizens that they’d like to move forward on. The meetings mentioned used swim lanes, a process mapping tool to map out the commencement process. The details to go on the swim lanes were acquired by the team leader, Kelly Vizanko, who emailed all of the stake holders and asked for their timelines. For the ones that were not received via email, they attended half-hour segments to help the team map out their part of the process. These meetings then identified areas of waste using kaizen bursts. From there the kaizen bursts were grouped based on the sub-process that they fell into and then later placed into a ICE Table, used for prioritization. This is how the kaizens were identified, by the most important/greatest impact, the level of control the team had, and by the ease to implement change/improvement. The kaizens identified were: Ticketing, Preparation, Volunteers, and Space + Configuration.
Ticketing consisted of eight people:
- Kelly Vizanko (Registrar’s Office) – Team Leader
- Ashley DeVoge (Ticketing Office) – Team Leader
- Megan Goke (Office of Continuous Improvement) – Facilitator
- Rylie Store (Office of Continuous Improvement) – Process Improvement Coordinator
- Alisha Kocjan (Registrar’s Office) – Team Member
- Shanda Miller (Bookstore) – Team Member
- Nancy Byers-Sprague (Graduate School) – Team Member
- Mary Stevens (Graduate School) – Team Member
This kaizen is wrapping up soon with a report out to the commencement committee. Several changes are expected such as scanning tickets to track the number of bodies in the room, communication to students (undergraduate and graduate) streamlined, established a limit for how many tickets will be issued, etc…
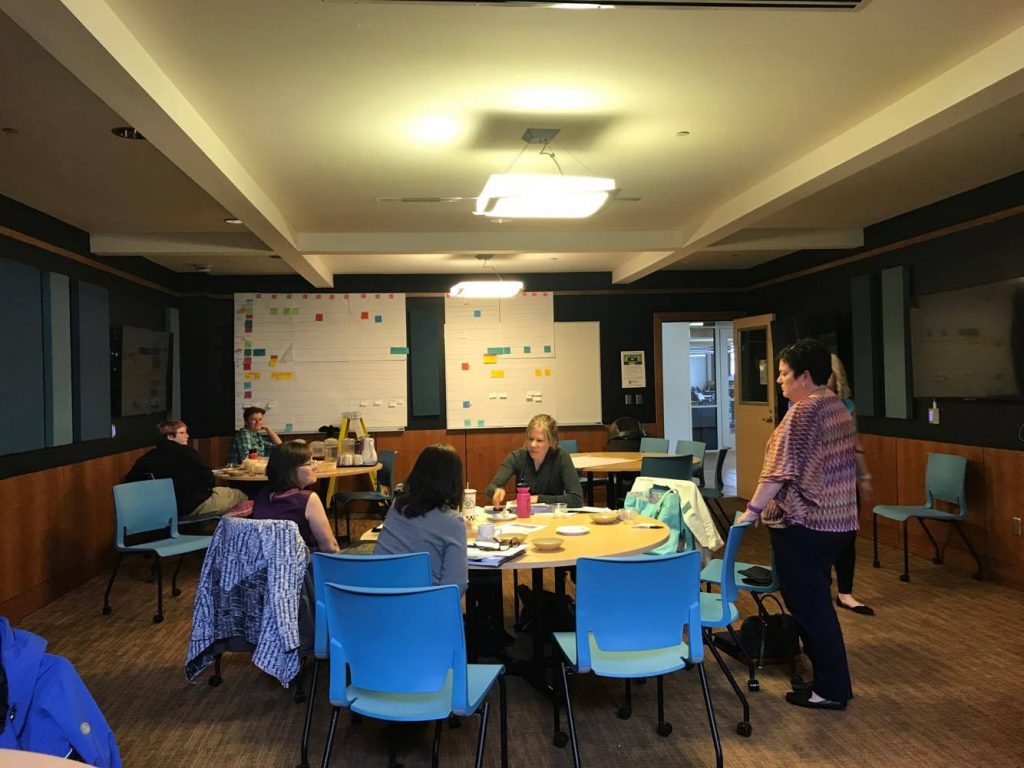
The Commencement Volunteers and Preparation kaizens are just about to take off, all we are waiting on is the dates to come (for the volunteer kaizen) and our team to be solidified for the preparation kaizen.
The team for volunteers is:
- Kelly Vizanko – Team Leader
- Gina LeMay (Research Office) – Facilitator
- Megan Goke – Facilitator
- Rylie Store – PIC
- Alisha Kocjan – Team Member
- Joel Isaacson (Athletics) – Team Member
- Jennifer Biekkola (Alumni House) – Team Member
- Brian Cadwell (Public Safety & Police Services (PSPS))- Team Member
- Daniel Bennett (University Safety & Security – PSPS) – Team Member
And to kick off the Preparation Kaizen we have:
- Kelly Vizanko – Team Leader
- Alisha Kocjan – Team Leader
- Laura Harry (Memorial Union) – Facilitator
- Rylie Store – PIC
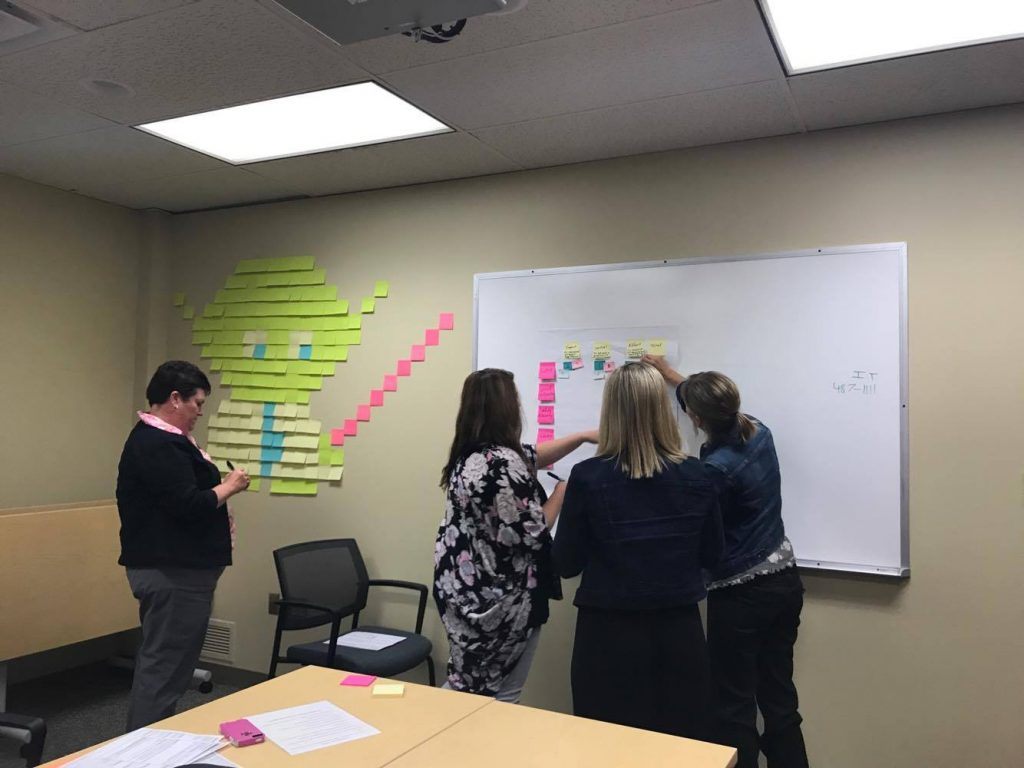
All in all, we have a ways to go on these kaizens but the goal is to have at least something changed in each of these areas by April 2018, and to reassess after this year’s commencement ceremony. A foot in the door for lean, just as the students are about to leave.