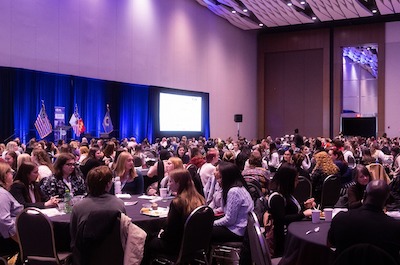
Five student members of the Society of Women Engineers (SWE) section at Michigan Tech and SWE advisor Gretchen Hein (MMET) attended the WELocal Detroit conference, held Saturday and Sunday (February 18–19).
The attending students were SWE President Aerith Cruz (junior, management information systems), seniors Lukas Pyryt (mechanical engineering) and Kathleen Pakenas (biomedical engineering), and second-year students Kathryn Krieger (environmental engineering) and Ella Merklein (biomedical engineering).
At the conference, Krieger and Merklein gave a presentation titled “SWE Section and Engineering Ambassadors Host K-5 Engineering Days.” Hein participated in a panel discussion titled “Journeys in Academia, The Perks and Challenges” with faculty from Kettering University.
“Attending the WELocal conference and presenting on our outreach programs was an empowering experience,” said Krieger. “It was a great opportunity to showcase the incredible work being done by our section and a reminder that by working together, we can make a meaningful impact on the next generation of engineers.”
“Being my first conference, I very much enjoyed attending the WELocal conference,” said Pyryt. “This was a chance for me to truly become an ally for SWE and learn more ways to support this organization. I am very thankful for all connections I gained at this conference, as well as new information gained in sessions helping push more to become a better engineer in the process.”
The section celebrated with the SWE-Wisconsin Professional Section the achievements of Andrea Falasco ’12 (BS mechanical engineering) who was selected as an Emerging Leader in Technology and Engineering (ELiTE). “It was great seeing my SWE friends again and meeting new ones at the conference,” said Falasco. “I am honored to be chosen for one of the New ELiTE awards and am grateful for those who nominated me. I learned a lot at the conference and hope to bring this insight back to work and home.”
The SWE section at MTU thanks our alumnae, corporate sponsors, and the College of Engineering for their support of our section and travel to conferences.
By Gretchen Hein, Advisor, Society of Women Engineers.