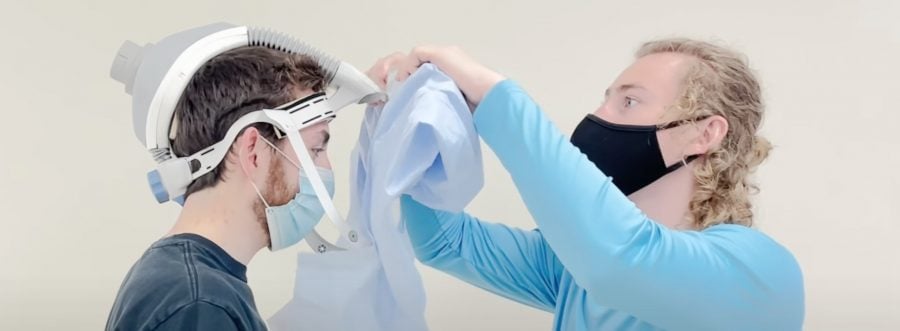
As we’ve come to expect, the judging for Design Expo 2021 was very close, but the official results are in. More than 1,000 students in Enterprise and Senior Design showcased their hard work on April 15 at Michigan Tech’s second-ever, fully virtual Design Expo.
Teams competed for cash awards totaling nearly $4,000. Judges for the event included corporate representatives, community members and Michigan Tech staff and faculty. The College of Engineering and the Pavlis Honors College announced the award winners below on April 15, just after the competition. Congratulations and a huge thanks to all the teams for a very successful Design Expo 2021.
Last but not least, to the distinguished judges who gave their time and talents to help make Design Expo a success, and to the faculty advisors who generously and richly support Enterprise and Senior Design—thank you for your phenomenal dedication to our students.
Please check out the Design Expo booklet and all the team videos.
ENTERPRISE AWARDS
(Based on video submissions)
- First Place—Husky Game Development (Team 115) Advisor Scott Kuhl, (CC)
- Second Place—Aerospace Enterprise (Team 106) Advisor L. Brad King, (ME-EM)
- Third Place—Innovative Global Solutions (Team 116) Advisors Radheshyam Tewari (ME-EM) and Nathan Manser (GMES)
- Honorable Mention—Consumer Product Manufacturing (Team 111) Advisor Tony Rogers (ChE)
SENIOR DESIGN AWARDS
(Based on video submissions)
- First Place —Advanced PPE Filtration System (Team 240) Team Members: Matthew Johnson, Electrical Engineering; Bryce Hudson, Mary Repp, Carter Slunick, Mike Stinchcomb, Braeden Anex, Brandon Howard, Josh Albrecht, and Hannah Bekkala, Mechanical Engineering Advised by: Jaclyn Johnson and Aneet Narendranath, Mechanical Engineering-Engineering Mechanics Sponsored by: Stryker
- Second Place—ITC Cell Signal Measurement Tool (Team 204) Team Members: Reed VandenBerg and Andrew Bratton, Electrical Engineering; Noah Guyette and Ben Kacynski, Computer Engineering Advised by: John Lukowski, Electrical and Computer Engineering Sponsored by: ITC Holdings Corp.
- Third Place—Development of a Beta Brass Alloy for Co-Extrusion (Team 234) Team Members: Anna Isaacson, Sidney Feige, Lauren Bowling, and Maria Rochow, Materials Science and Engineering Advised by: Paul Sanders, Materials Science and Engineering Sponsored by: College of Engineering
- Honorable Mention—EPS Ball Nut Degrees of Freedom Optimization (Team 236) Team Members: Brad Halonen, Rocket Hefferan, Luke Pietila, Peadar Richards, and David Rozinka, Mechanical Engineering Advised by: James DeClerck, Mechanical Engineering- Engineering Mechanics Sponsored by: Nexteer
- Honorable Mention—Electric Tongue Jack Redesign (Team 230) Team Members: Jack Redesign and Brandon Tolsma, Mechanical Engineering; Collin Jandreski, Christian Fallon, Warren Falicki, and Andrew Keskimaki, Electrical Engineering Advised by: Trever Hassell, Electrical and Computer Engineering Sponsored by: Stromberg Carlson
- Honorable Mention—Bone Access and Bone Analog Characterization (Team 212) Team Members: Sarah Hirsch, Mechanical Engineering; Elisabeth Miller and Christiana Strong, Biomedical Engineering; Morgan Duley, Electrical Engineering; Katelyn Ramthun, Biomedical Engineering Advised by: Hyeun Joong Yoon and Orhan Soykan, Biomedical Engineering Sponsored by: Stryker Interventional Spine Team
- Honorable Mention—Blubber Only Implantable Satellite Tag Anchoring System (Team 221) Team Members: Quinn Murphy, Lidia Johnson, Joshua Robles, Katy Beesley, and Kyle Pike, Biomedical Engineering Advised by: Bruce Lee, Biomedical Engineering; Sponsored by: NOAA
DESIGN EXPO IMAGE CONTEST
(Based on image submitted by the team)
- First Place—Blizzard Baja (Team 101): “Our current vehicle, Hornet, after a race.” Credit: Blizzard Baja team member
- Second Place—WAAM Die Components (Team 237): “MIG welding robot printing a steel part.” Credit: Mike Groeneveld
- Third Place—Aerospace Enterprise (Team 106): “Team photo, pre-Covid.” Credit: Aerospace Enterprise team member
DESIGN EXPO INNOVATION AWARDS
(Based on application)
- First Place—Consumer Product Manufacturing Enterprise, Shareable Air project (Team 101) Advised by: Tony Rogers, (ChE)
- Second Place—ITC Cell Signal Measurement Tool (Team 204) Advised by: John Lukowski (ECE)
- Third Place—Hospital Washer Autosampler Implementation (Team 218) Advised by: Sang Yoon Han and Houda Hatoum (BioMed)
DESIGN EXPO PEOPLE’S CHOICE AWARD
(Based on receiving most text-in voting during Design Expo)
- Consumer Product Manufacturing, CPM Advised by: Tony Rogers, (ChE)
ENTERPRISE STUDENT AWARDS
- Rookie Award—Jack Block, CFO – Supermileage Systems Enterprise
- Innovative Solutions—Cody Rorick, Alternative Energy Enterprise
- Outstanding Enterprise Leadership—Andy Lambert, CEO – Supermileage Systems Enterprise and Daniel Prada, Spark Ignition (SI)
- Team Lead—Clean Snowmobile Enterprise
ENTERPRISE FACULTY/STAFF AWARDS
- Behind the Scenes Award—Kelly Steelman, Associate Professor and Interim Chair, Dept. of Cognitive and Learning Sciences, nominated by Built World Enterprise.