By Megan Johnson, Student Process Improvement Coordinator
This summer while I was at Caterpillar, I had the opportunity to train and test for my Six Sigma Green Belt. In the Six Sigma improvement methodology, there are belts that, similar to karate, indicate a level of expertise or experience. Yellow Belts have basic training; Green Belts learn more about Six Sigma tools and participate in CPI (Continuous Product/Process Improvement) or NPI (New Product/Process Introduction) projects. Black Belts and Master Black Belts have more advanced Six Sigma training and devote 100% of their time to improvement through Six Sigma. My Green Belt training was in the DMAIC methodology.
DMAIC means:
Define: Define the problem, the Voice of the Customer (VOC), and goals.
Measure: Measure, collect data.
Analyze: Analyze the data and seek the root cause of the problem.
Improve: Improve the process or product—identifying the countermeasure(s).
Control: Control the future state—create a visual workplace, monitor the product/process, etc.
Having had a Lean background prior to my 6 Sigma Green Belt training, I felt that the DMAIC methodology correlated well to the Four Step Problem Solving Process that is used in Lean Kaizen Events.
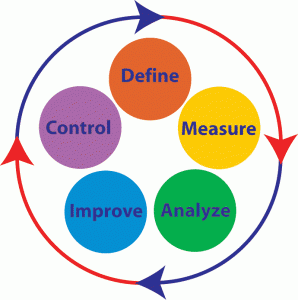