We are pleased to present this guest blog by Rick Berkey, Research Engineer II and Product Development Manager, as well as a campus Lean Facilitator.
I recently purchased a lawn dethatcher online and was anxious to assemble it when I got home from work yesterday. When I opened the package, I was expecting the usual bag of parts and fasteners that fly everywhere when you rip open the industrial strength plastic packaging. If you’re like me, you also know instructions can be more like ‘suggestions’ — you look at bad illustrations, use your judgment, sort through parts that look close enough, skip important steps because you think you know the correct way, then take things apart once you realize you really don’t… and of course you end up with missing pieces or extra parts that you store as ‘just in case’ inventory. If only we had enough ‘junk drawers’ in our homes!
Instead, I was pleasantly surprised to find a great application of Lean (see image). All parts and fasteners are arranged on a ‘shadowboard’. Each panel was clearly labeled according to the sequential assembly steps provided in the instruction sheet. This simple yet effective solution highlights several Lean principles. First, it is centered around defining value in the eyes of the customer – i.e. making it easier for the person assembling it. Second, it embraces the 5S concept of establishing ‘a place for everything and everything in its place’. Third, it serves as an effective visual control for the assembly process.
As the customer, I experienced several benefits and hence derived value as follows:
1. Knowing I had all the parts BEFORE I began…and if for some reason a part were missing, it would be obvious at the start
2. It was difficult NOT to follow instructions…the shadowboard keeps you on task. This can also be seen as an example of Poka-Yoke or mistake proofing
3. Faster assembly time, by reducing the following wastes: motion (looking for parts), defects (using wrong parts for a given step)
4. No missing/extra parts at the end…wow!
Kudos to Brinly-Hardy for getting it right with their product. The time and aggravation I saved was channeled into USING the product…after all, the goal was to dethatch my lawn, not assemble a dethatcher. Now, I know we’re not assembling dethatchers here on campus (well, maybe the Grounds department is!), but I would challenge all of us to see how these principles can and do apply to the things we do every day. Some questions to consider in your daily work: Who is your customer, and how to they define ‘value’? Is your work helping to create value or is it creating additional waste? Is there a visual solution that can streamline the process? When you develop and improve work processes, have you considered mistake proofing methods to make it easier to do it right the first time (by making it hard to do it incorrectly)?
Feel free to comment, and in the meantime I need to finish raking all that dead grass!
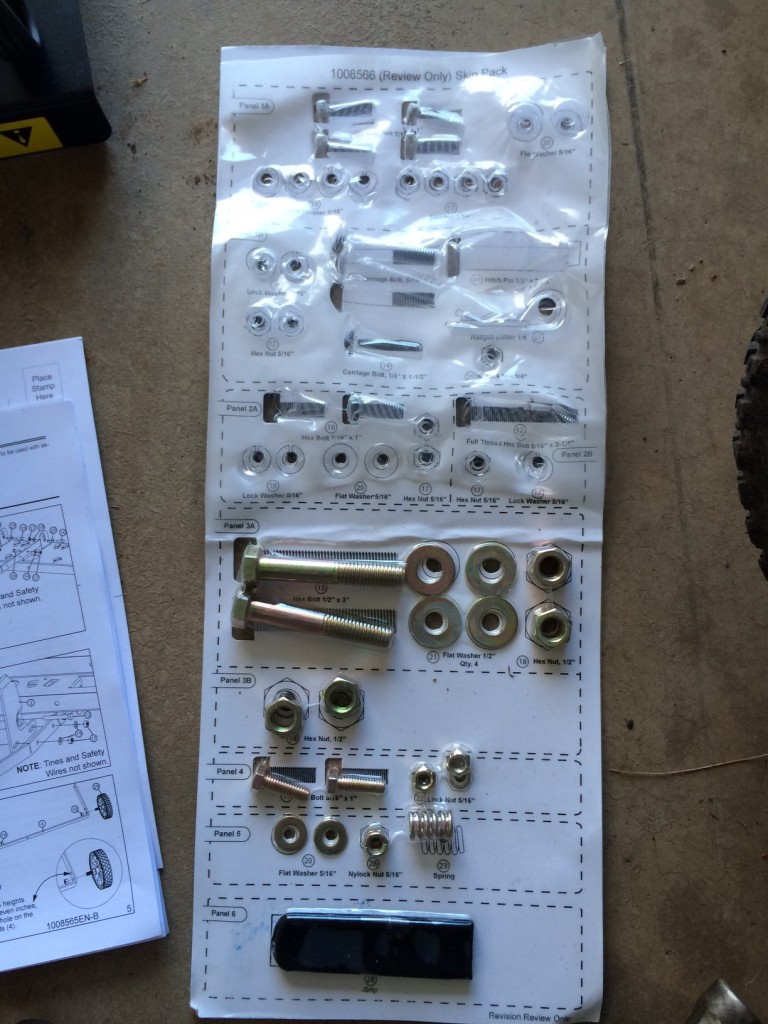