Our University recently switched to a new compact toilet paper from Georgia Pacific. Being a Lean practitioner, I have thought about this toilet paper change every trip to the bathroom since. I think of each instance of waste that was eliminated from the simple change in design of the toilet paper roll.
On the right you have your standard toilet paper roll…..and on the left is the new type of toilet paper we are using:
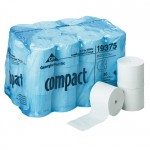
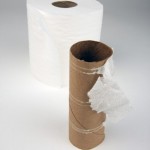
I have compiled some of my best thoughts on the major waste reductions from this new toilet paper roll design, though I cannot be certain that all are recognized by the stakeholders:
- Inventory reduction – less space required for storage of inventory, more inventory per square foot.
- Over Processing (doing more than necessary to produce a product or service) – As a customer I never used the cardboard roll and this new toilet paper design appears to be working just fine without it. Thus, it was unnecessary.
- Motion/Movement – I assume there is less changing of toilet paper as there is more “TP” per roll. There will also be more rolls shipped per delivery truck!