This week I had the privilege of attending the First Annual Copper Country Lean Conference at Michigan Tech. Now I’m not going to lie I went into this conference not expecting much and was prepared to just be talked at all day but, it ended up being so much more. Ever since starting this job, I have become significantly interested in Lean and Continuous Improvement. It has helped me figure out how to study in a way that benefits me, plan out trips, and organize almost every aspect of my life. However, until the conference I never really understood the meaning or feeling of being involved in a Lean Community. I mean, I understood that there were people around me who were also passionate about Lean and that I could be considered a part of the Michigan Tech Lean community, but during the conference I was able to see what that truly meant.
At the conference there were people from all different industries and from all across the Keweenaw and further. These people had different jobs, degrees, and interests, but there was one thing everyone had in common, their interest in lean. Some people had been practicing lean for years, while others had just begun their lean journey, but it didn’t really matter. During this day everyone networked and shared stories of how lean has impacted them, or how they plan to integrate lean into their lives. Ideas were being bounced around and contact information was being shared. It was crazy to me how one thing, Lean, could connect so many people who have so many differences.
It’s when I saw all of these people interacting, sharing stories, and really being engaged in the conference I realized how much Lean really can connect you with others. It also showed me how important it is to develop your “community of practice” with in Lean. If you have that group of people eager to share their knowledge with you it allows you to grow as a lean practitioner and expand your own understanding of lean through theirs. So, this week I really felt what is was like to be a part of a Lean community.
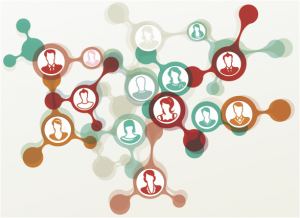