So often we get caught up in our projects: we start them, prioritize them, and then devote all of our attention to them one by one until they’re completed. We very rarely have a single project that is on-going for a long period of time; why is this?
I think it’s because we don’t want lingering work, we thrive off of completion. From that we gain satisfaction and pride in our work.
There is, however, a trade-off for this pride. That is, when we continuously move from one project to the next, seeing each to completion before starting the next, most of us quickly become burned out. When we get burned out we lose our energy and our enthusiasm, as well as become negative, frustrated, and unproductive. That satisfaction we were chasing before no longer sustains us.
Back in February, one of my co-worker’s blogged on incremental improvement, and recently she blogged about Preemptive Improvement. In these blogs, she’s shared how our office has been using small improvements to achieve a high future state and strive for perfection, even when a correction isn’t necessary. These methods are some that I’ve been applying in my own personal life heavily in the last year or so.
Last July I got engaged, we set a date 11 months out and so commenced the wedding planning. For all those who’ve been married, you probably know the magnitude of this task. I’ve always been a “planner,” per say, and I tend to enjoy getting to use my creativity, so from the beginning I’ve been pretty excited about the planning process. However, I know a lot of people who’ve gotten married and I’ve learned that the entire process isn’t always fun, or creative. I also know myself and I tend to go and go and go, and focus on one thing until it’s complete before I’ll start the next; meaning, I tend to burn myself out.
Knowing the planning wouldn’t always play on my interests, and knowing that I sometimes overburden myself were good things to be aware of back in July. Because of this, I was able to plan ahead and use my lean thinking skills to combat potential burnouts or becoming a bridezilla (my worst nightmare). I did this by utilizing the skills I’ve learned here in the Office of Continuous Improvement. I can honestly, say with 10 days left until the wedding, that I’ve only had two “burnouts,” one as a result of over-processing, and the other was out of my control to change.
After talking to multiple soon-to-be wives, I’ve learned that I am the one who’s been the least bit stressed about the planning process as a whole and I believe this is from all of the lean I’ve implemented… From organizing my thoughts via a gigantic affinity diagram, laying out the roles and responsibilities of our family members in a swim lane, using a decision matrix to decide on venues and vendors, ICE prioritization of tasks, plentiful checklists, recognizing when I was over processing, and also taking it one step at a time and remembering that the entire wedding doesn’t need to be planned over-night.
I’ve also gathered that on average, the last three weeks before the wedding tend to be the busiest with wrapping up small details. However, because of the prioritization that we conducted early on, and the small deadlines we set, we were able to spend two of those weeks towards something not related to wedding, and only spend the last week wrapping up details.
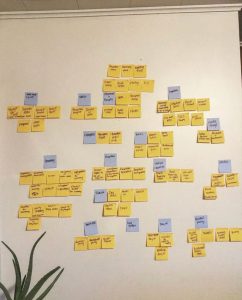
The purpose of today’s blog post is to show you that as long as you learn how to slow down your thinking, anyone can implement and benefit from small improvements striving for perfection.