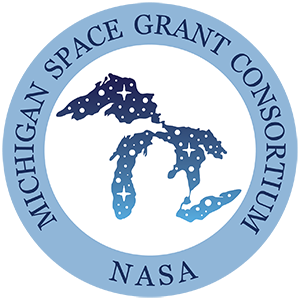
A diverse, multitalented group of Michigan Tech students, faculty and staff members have been awarded fellowships and grants totaling an impressive $55,701 from the Michigan Space Grant Consortium (MSGC) for its 2022-23 funding cycle. This funding is sponsored by NASA.
Seismic amplitude-based lahar tracking, agriculture and food security, the effects of heavy metals on vegetation, and job shadowing aerospace and earth systems careers: these are just a few of the exciting, innovative projects that received funding.
The MSGC reflects NASA’s interests and promotes awareness, research and education in “space-related science and technology in Michigan.” To achieve this goal, the consortium not only funds fellowships and scholarships for STEM students, but also financially supports curriculum enhancement and faculty development. The MSGC is also deeply committed to supporting and upholding NASA’s policy of diversity and inclusion.
Congratulations to the winners and best of luck on your projects.
Thank you for representing Michigan Tech and making our University community proud!
Michigan Tech undergraduates who received $4,000 research fellowships are:
- Brendan Harville (GMES) — “Seismic Amplitude-Based Lahar Tracking for Real-Time Hazard Assessment” with Greg Waite (GMES)
- Sierra Williams (CFRES) — “Understanding the Controls of Solute Transport by Streamflow Using Concentration-Discharge Relationship in the Upper Peninsula of Michigan” with Fengjing Liu (CFRES)
Michigan Tech graduate students who received $5,000 research fellowships are:
- Espree Essig (GMES) — “Analyzing the Effects of Heavy Metals on Vegetation Hyperspectral Reflectance Properties in the Mid-Continent Rift, USA” with Chad Deering (GMES)
- Caleb Kaminski (GMES) — “Investigation of Ground-Penetrating Radar Interactions with Basaltic Substrate for Future Lunar Missions” with Aleksey Smirnov (GMES)
- Katherine Langfield (GMES) — “Structural Characteristics of the Keweenaw and Hancock Faults in the Midcontinent Rift System and Possible Relationship to the Grenville Mountain Belt” with James DeGraff (GMES)
- Tyler LeMahieu (CEGE) — “Assessing Flood Resilience in Constructed Streambeds: Flume Comparison of Design Methodologies” with Brian Barkdoll (CEGE)
- Paolo Rivera Gonzalez (GMES) — “Impacts of La Canícula (“Dog Days of Summer”) on Agriculture and Food Security in Salvadoran communities in the Central American Dry Corridor” with Kari Henquinet (SS)
- Erican Santiago (BioMed) — “Perchlorate Detection Using a Graphene Oxide-Based Biosensor” with Hyeun Joong Yoon (BioMed)
- Kyle Schwiebert (Math) — “LES-C Turbulence Models and Their Applications in Aerodynamic Phenomena” with Alexander Labovsky (Math)
Michigan Tech faculty and staff members who received $2,200 or more for pre-college outreach and research seed programs are:
- Paul van Susante (ME-EM) — Hands-On NASA-Oriented Experiences for Student Groups (HONES): “Lunabotics Competition Robot”
- Jannah Tumey (Center for Educational Outreach) — “Tomorrow’s Talent Series: Exploring Aerospace & Earth System Careers Through Virtual Job-Shadowing”
- Xinyu Ye (CEGE) — “Analyzing the Effects of Potential Climate and Land-Use Changes on Hydrologic Processes of Maumee River Watershed Using a Coupled Atmosphere-Lake-Land Modeling System”
By the Graduate School and Shelly A. Galliah.