The first lean project I assisted has finished up its first phase. I worked with Eric Karvonen, Executive Chef and Kathy Wardynski, Manager of Purchasing and Process Improvement on a shelf that holds catering bowls and utensils inside the MUB kitchen. We used 5S methodology to tackle the current state problems.
On the first day we took a look at the current state: lots of clutter, lack of organization and no system to sustain any organization that is attempted. To begin work we removed any items from the shelf that should not have been there. All of these items already had a proper place to be stored, but had accumulated on this shelf. Next, we began trying different arrangements of the bowls and utensils that would remain. After consulting a few subject matter experts (catering staff, dish washing staff) a final arrangement was agreed upon. Along with the organization, the fluid ounce capacity of each size of bowl was determined to make bowl selection easier during food preparation for catering.
Before the next visit to the pebble bowl shelf, labels were created for the new organization. The next day consisted of applying duct tape to section off parts of the shelf for each of the bowl sizes and utensils. The labels were applied for each position to sustain the new current state.
Overall, this phase of the project went great. Future phases of the project will continue throughout the summer, next we will begin work on the storage of catering trays as well as various sauces, oils, and vinegars.
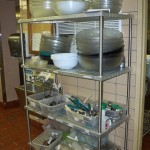
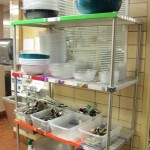