By Megan Johnson, Student Process Improvement Coordinator
Data collection is an important element when making improvements because without it there is lack of “evidence” that a problem exists. Why are you improving? Is it really a problem? Many times “problems” are exaggerated by feelings and frustration. Often times the frustration is related to symptoms of what the root problem is.
If there is a concern about a process, data-collection can be used to paint a picture of the “current state” and provide insight into current issues and hone in on where improvements should focus. A recent kaizen event for navigating the Memorial Union Building (MUB) is a good example of the importance of having that baseline data. It seemed that a lot of guests in the building would stop in various offices to ask for directions to different meeting rooms. Interruptions can be frustrating for employees, but was navigating the MUB a problem for guests?
Data collection began to identify the frequency a guest would stop and ask a MUB staff member for directions to their meeting room. Also, where did the guest enter the building and what room were they looking for? After the data confirmed that there was an issue, a kaizen event took place on November 28 to analyze the data to identify improvements. A team identified countermeasures to reduce/eliminate the navigation problem and is currently implementing them. They will continue to collect data to gauge the success of the changes.
Click here to learn more about Metrics and Data Collection.
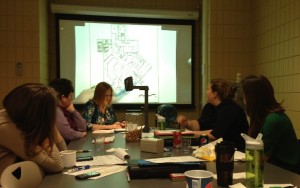