If you’ve been following our blog for a little while, you’re probably already aware of this. I have been with the Office of Continuous Improvement here at Michigan Tech for a little over a year and a half. The last year of that has been spent training in new student Process Improvement Coordinators at a regular speed. In the past year we have put four people through our training completely, and our fifth will be wrapping up within the next few weeks. Our first guinea pig was Stephen, then we had Anita, and Ari. After Ari, there was enough data and feedback to dedicate some time (upwards of 45 hours) to making revisions, deletions, and additions to the training. Then Matt joined our crew, our Guinea pig for the second round, and currently we have Blake going through the training (he will formally introduce himself in a few weeks). All five of these people have brought a great deal of joy, excitement, and “proud parent” moments for me as I watch them move through different modules, emotions, and faces.
What’s interesting is they all seem to have identical emotions but how they react to their emotions has been incredible for me to watch. I can almost now tell where Blake is at in the training without checking online to see his progress, simply by watching the vibe he’s giving off.
Moving back a year, I was assigned to redesign the training along side my co-worker at the time, Aspen. We sat down and discussed what worked and didn’t work from the training we went through. We talked about all the things we wish we had known, and the questions we asked. This started our direction for drafting the new training course. Then we hit a rut. “What is our goal? What does our future state look like. ” It took us a long time (I mean a few weeks) to answer this question. Then one day it was clear as day, duh! We want to design a training course that eliminates the surface questions, promotes deeper questions, and provides the new PIC with everything they need to know or how to find out what they need to know to jump into our processes. Once this was established we took off running.
In the past four months I have spent about 75 hours updating the training to get closer and closer to our future state. We will have to take several more jumps but we’re closer.
The piece about training others that is so rewarding for me is that, through these new comers, I am able to relearn lean again and again. I’m able to experience the flood and being overwhelmed, the light bulb flickering on, and the excitement once you finally get it! Its breath-taking to have this opportunity repeatedly, and this, this helps me to see a clearer picture of what our next jump is. Plus, then I have more minds to help pull it off. 🙂
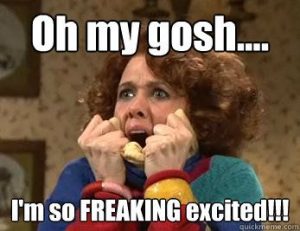