You might recall a post from almost one year ago when I introduced the concept of personal kanban boards. I began using this tool that week and I have not gone a day without using my board since! I find this tool to be very effective for my work (projects, correspondence, coordination of activities, etc.).
If you compare the below picture to the graphic in the 2012 blog post you will see that my personal kanban has evolved quite a bit – a little bit of check and adjust. I have made many changes over this past year to adapt the board to fit my needs, I think this is a very important step in making your kanban board work for you.
Here is a bit about some of the changes I made to my board:
- I color coded my work (stickies) by month – giving each month a color allows me to see items that are falling behind. A month works great for the type of work I do.
- I changed my headings – the original PDCA heading was more confusing than helpful (personal opinion, I know others who find these headings to work well). I came up with three headings: my “hopper” are items I will work on at some point, “today” is work items for the day, and my “waiting” column allows me to keep track of items that I sent off but will be waiting for a response on.
- I also strategically limited my column sizes. For instance, my “today” column cannot fit more than five stickies. I would despise working a day with more than five stickies – so this board constraint holds me to that. Limiting your work in process (WIP) is one rule for personal kanban. The other rule is to visualize your work.
In the past year, I also found a great website that helped me better understand this concept: http://www.personalkanban.com/pk/.
If you are interested in starting a personal kanban board for yourself or your work group, please contact me. We have many examples across campus to give you some ideas.
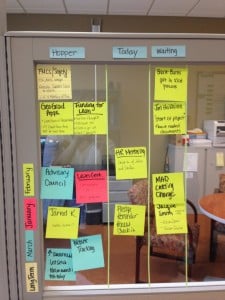