- Amanda Cadwell (Administrative Aide, Civil/Environmental Engineering & UAW President)
- Wendy Davis (Manager of Process Improvement)
- Bob Hiltunen (Director, Auxiliary Services)
- Ellen Horsch (Vice President for Administration)
- Rhonda McClellan (Facilities Helper, AFCSME member)
- Barb Ruotsala (retired, past UAW President).
Brittany Wood, Market Research Analyst Intern and I began working on an article that was to discuss the Lean “journey” Michigan Tech’s Dining Services has experienced over the past four years. After lots of research, interviews, and multiple drafts the article was completed in October.
The Business Officers magazine has published the article in their February edition! The article is the feature piece in the Business Intel section of the magazine.
Special thanks to Kathy Wardynski, Ellen Horsch, and Bob Hiltunen for letting us interview them on multiple occasions, and to Ann Kitalong-Will, Wendy Davis, Megan Johnson, Ellen Horsch, and Gina Sayen for reviewing and editing the many drafts of the article.
You can read the article online, or contact Wendy Davis to borrow a copy of the magazine out of the Lean Library.
By Megan Johnson, Student Process Improvement Coordinator
Data collection is an important element when making improvements because without it there is lack of “evidence” that a problem exists. Why are you improving? Is it really a problem? Many times “problems” are exaggerated by feelings and frustration. Often times the frustration is related to symptoms of what the root problem is.
If there is a concern about a process, data-collection can be used to paint a picture of the “current state” and provide insight into current issues and hone in on where improvements should focus. A recent kaizen event for navigating the Memorial Union Building (MUB) is a good example of the importance of having that baseline data. It seemed that a lot of guests in the building would stop in various offices to ask for directions to different meeting rooms. Interruptions can be frustrating for employees, but was navigating the MUB a problem for guests?
Data collection began to identify the frequency a guest would stop and ask a MUB staff member for directions to their meeting room. Also, where did the guest enter the building and what room were they looking for? After the data confirmed that there was an issue, a kaizen event took place on November 28 to analyze the data to identify improvements. A team identified countermeasures to reduce/eliminate the navigation problem and is currently implementing them. They will continue to collect data to gauge the success of the changes.
Click here to learn more about Metrics and Data Collection.
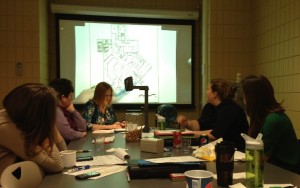
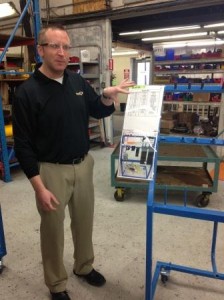
I had the opportunity to take a tour of Pettibone in Baraga, MI earlier this week. Pettibone is currently working on incorporating Lean practices into its operations, and they are one of 12 local business in Houghton County that make up a group that we have coined the “Local Lean Group.” We have been meeting every few months to learn from each other. In the picture above, Scott is showing a cart that you or I could walk into the plant and complete without flaw. They have highly visible, standardized operations and practices (which result in fewer mistakes and serve as a platform form even more improvement). If you are interested to learn more about our group, give me a call or send me an email
By Kaylee Betzinger, Student Process Improvement Coordinator
Lean Training funded by a grant from the Federal Mediation and Conciliation Service (FMCS) has been going on for the past several months. November 5th and 6th marked the last FMCS Lean Training sessions here on campus with our consultants, Mike Taubitz and Larry Osentoski. Two cohorts of employees completed Lean training:
- Lean Facilitators – trained to facilitate Kaizen Events for any campus department or area interested in making improvements.
- Lean Implementation Leaders – trained in Lean concepts aimed at building a Lean practice into the day-to-day work for an area or department.
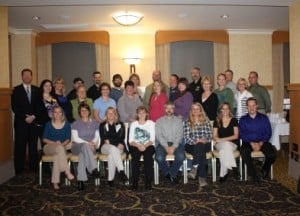
During the last training sessions each trainee participated in a Kaizen Event. The Lean Implementation Leaders chose a problem within their department for teams to work through and the Lean Facilitator teamed up to practice their Kaizen Event facilitation skills.
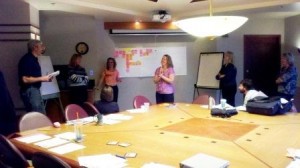
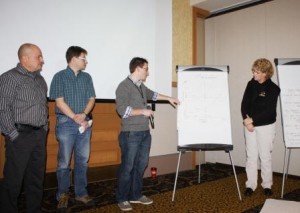
Each trainee had their own personal experience with the training. There were many laughs among the group and a lot of great memories. Some of the trainees share some of their experiences:
- Rachel Wussow: “When learning Lean tools and thinking Lean, I am challenging and improving myself as a professional. My customer is an 18 year old college student. So, I have to teach the Lean lessons to a different generation of thinkers. Lean is more than improvement it is sustaining and acting. The world is full of change and Lean is a tool of adjustment.”
- Cat Burns: “My first experience was very positive. I enjoyed working with people that I may not normally interact with. It felt great to officially start my involvement with Michigan Tech’s Lean Journey. I was lucky to have two great (and original) Facilitators work with me on my first Kaizen.”
Thank you to all our trainees, our consultants, and Manager of Process Improvement, Wendy Davis for making these training sessions so enjoyable and valuable!
By: Puneet Kumar Vasudev
Continuous improvement is an ongoing effort to improve products, services, or processes. These efforts can seek “incremental” improvement over time or “breakthrough” improvement all at once. Delivery (customer valued) processes are constantly evaluated and improved in the light of their efficiency, effectiveness and flexibility. I work as a student process improvement coordinator at Auxiliary Services. I have been working on an improvement project with Kathy Wardynski, Manager or Purchasing and Process Improvement, looking at fryer oil consumption. Wadsworth Hall was consuming more than twice the amount of oil as compared to the oil consumption of any of the residential halls when the figures of oil consumption per number of students catered was compared.
According to the work instruction at each work station in Wadsworth Hall, fryer oil is cleaned daily during the last shift and the oil is changed on every Saturday, if needed. The oil change instructions require a dip test with a tester in which a paper strip is dipped in oil and the color on the strip left by the oil is compared with the chart to indicate whether it is fit for use or not. This practice was not being followed effectively. This led to two different situations, either the oil was being changed even if it would have been good for 3-4 more days or oil change was delayed leading to bad food quality.
Since oil quality measurement was a concern, it was decided to remove the ambiguity related to existing oil testing method, with a new digital oil tester. In addition to the new tester, a data capture sheet was drafted to monitor the deterioration in oil condition and oil changes of different work stations. Oil is now changed as needed, at any given day of the week. Through the data collection at Wadsworth Hall we hope to come out with new data and figures to implement more improvements with fryer oil consumption.
It is estimated that the small changes made will save $5,000 per year in fryer oil consumption at Wadsworth Hall.
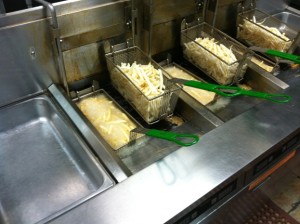
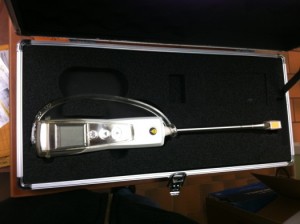
Recently, Assistant Vice President for Administration, Theresa Coleman-Kaiser was interviewed for a Radio show on Michigan Business Network’s website . Theresa spoke about our Lean Journey and how Lean principles are becoming more widly practiced here at the University.
Click HERE to listen to her interview.
Blog post written by: Kaylee Betzinger, Student Process Improvement Coordinator
Metrics boards are used to showcase an area’s leading performance indicators and valued or strategic goals. Over the past few weeks, staff in each residence hall kitchen have been working together to standardize metric board layout and eliminate the “waste” associated with the current state of their boards (or lack of boards).
The 5S methodology was utilized to see this project out. Sorting through the metrics that were currently being displayed, creating an order, shining (purchasing new boards where needed), and a weekly rotation schedule to insure all the metrics get updated each week (sustain).
There are now metrics boards, as well as safety boards, in each of the halls. Metric boards track food waste in dollars and pounds, inventory on hand, and other key performance indicators. The safety boards track days without incident and display lockdown and evacuation procedures, weekly operating reports, and monthly kitchen safety inspection sheets. With the new metrics boards in place, there is less confusion amongst staff and key performance indicators are reinforced. It is also recommended that Daily Team Meetings take place at the metrics board.
Take a look at some of the before and after pictures from this project:
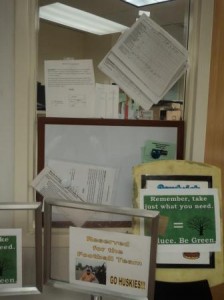
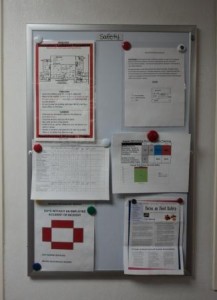
A quick improvement event was held last week at the Portage Lake Golf Course. Below are some pictures from a ride we took on the course – a trip to the gemba (where the work is done). Golf Course staff – managers, mowers and maintenance – along with some outside eyes were brought together to investigate fluctuating fuel use (gallons) from season to season. The team did some inventory and data collection during the kaizen to understand where the fuel was being used (flip chart picture below).
As a result of the kaizen, refueling standards were put in place: holding tank refuel schedule every 2-3 weeks and a full refuel of all machines and holding tank at the end of each season. In past years, the tank was refueled when empty and not consistently at the end of each season (i.e. a lapse in full refuel in season A would cause a substantial increase in gallons in season B). This new standard will provide a consistent fueling schedule season to season, a first step to being able to better forecast fuel costs. Other causes for fuel fluctuations will continue to be investigated – mowing sequence and patterns (movement waste, over processing) , idling times (waiting waste: working around customers on course, moving benches, etc.) and maintenance of machines (correction waste). To learn more about the types of waste, you can download the Learning to See Waster PowerPoint HERE.
The best outcome of this quick kaizen was that the staff left with inspiration to beging working on the other improvement opportunities!
I participated in my first kaizen event last week. The cause for the kaizen was to identify a standardized process for frying and grilling items in the MUB Food Court. There was no set process which caused employees to make instinctive decision that sometimes resulted in too much or too little product for the customers.
We began with some data collection and analyzing the current situation. With an understanding of what currently was happening we brainstormed what we would like the future state to be. We then did a lot of data collection: cooking times for all of the grill items (thawed and unthawed timing) and then taste tests after intervals under the warmer to note poor quality intervals. This data allowed us to set a standard for each items cooking time and holding time.
Matt Lean, who led this kaizen, had some data regarding which grilled/fried food items were sold at different time periods throughout the day from previous months of data collection. As a team we had to evaluate the data so we could find the average items sold at different 15 minute increments. One of the bigger and time consuming problems was which method to use to find these averages. It took us a good chunk of time and a check and adjust process to figure out which way worked best and in the end we were able to see the averages and come up with some possible solutions to our initial problem.
In the end we had a solid start on our new standardized process, as well as visuals for both the workers and customers to see (max hold times, cooking times for each item, “Grad n’ Go”, “Please Order Here”, “Don’t see what you’re looking for? Please Ask!”). My favorite part about the whole experience was getting to see others learn and experience lean. By the end of the kaizen the whole team had a good understanding of Lean thinking and how the kaizen approach works. We all got to see firsthand how beneficial this type of thinking is.
–Kaylee Betzinger, Student Process Improvement Coordinator