For some people accomplishment comes from the words, “our work here is done,” however, I believe that accomplishment can also come from, “we’ve only just begun.”
As we’ve shared in the past, each year 15-18 Michigan Tech faculty and staff come together in hopes of becoming the newest additions to our facilitator co-hort here on campus. To achieve the title of a “Level 1 Facilitator,” each candidate must attend seven days of training, complete various homework assignments, and participate as either a team leader or a facilitator on a new kaizen with three to four other candidates.
The group I’ve been assigned to has decided that their kaizen was going to be to 5S the Foundry Lab located in the Material Science and Engineering building. A couple of weeks ago, four future graduates, and an already seasoned facilitator, went to the gemba, where work is done. Our tour of the Foundry Lab consisted of Team Leader, Matthew Otte (Material Science and Engineering) walking us through the various workstations and processes for every corner of the lab. Our walk took a little over an hour and a half, and we really only scraped the surface for potential areas of improvement.
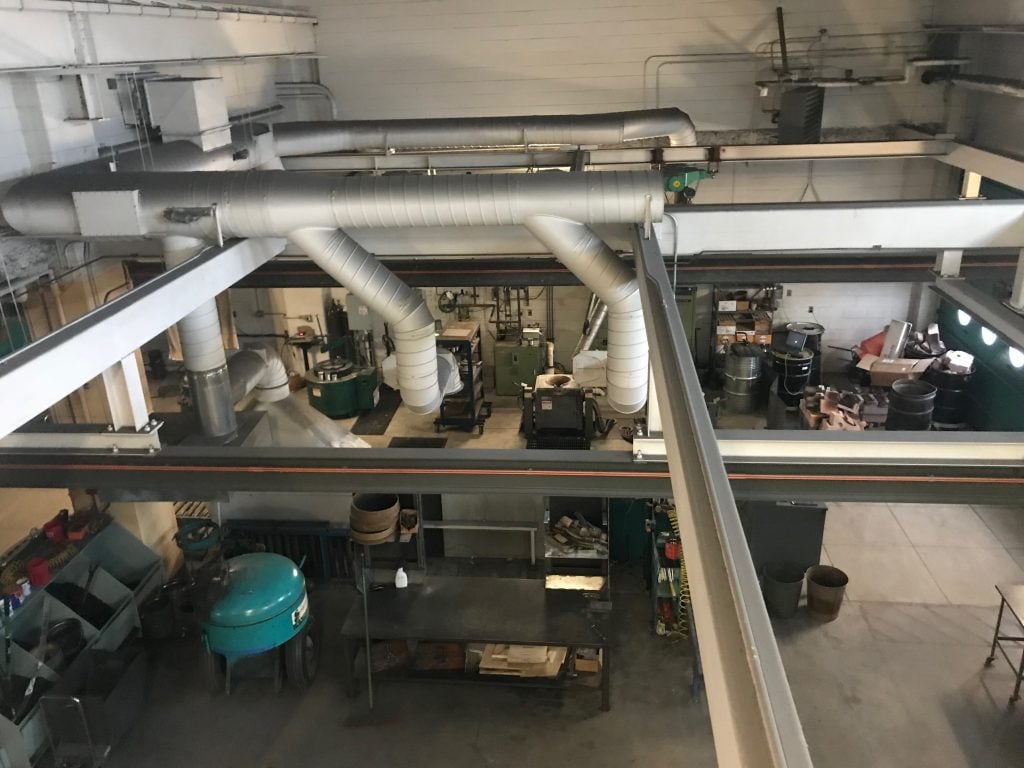
Following this Gemba walk I found myself a little overwhelmed by the magnitude of potential within the lab. I was struggling with imagining where, how and when to start.
One of my favorite things about lean is that it has taught me to become an independent problem solver. When this overwhelming feeling creeped in I remembered that the most important thing with any change is to just start. There’s no rule that says you must jump from current state to ideal state in one step. Continuous Improvement is about incremental changes. It doesn’t matter how big the stride, what matters is the direction.
Considering this, the team and I regrouped, and we decided to start with one single workbench and slowly pick away at other areas within the Foundry.
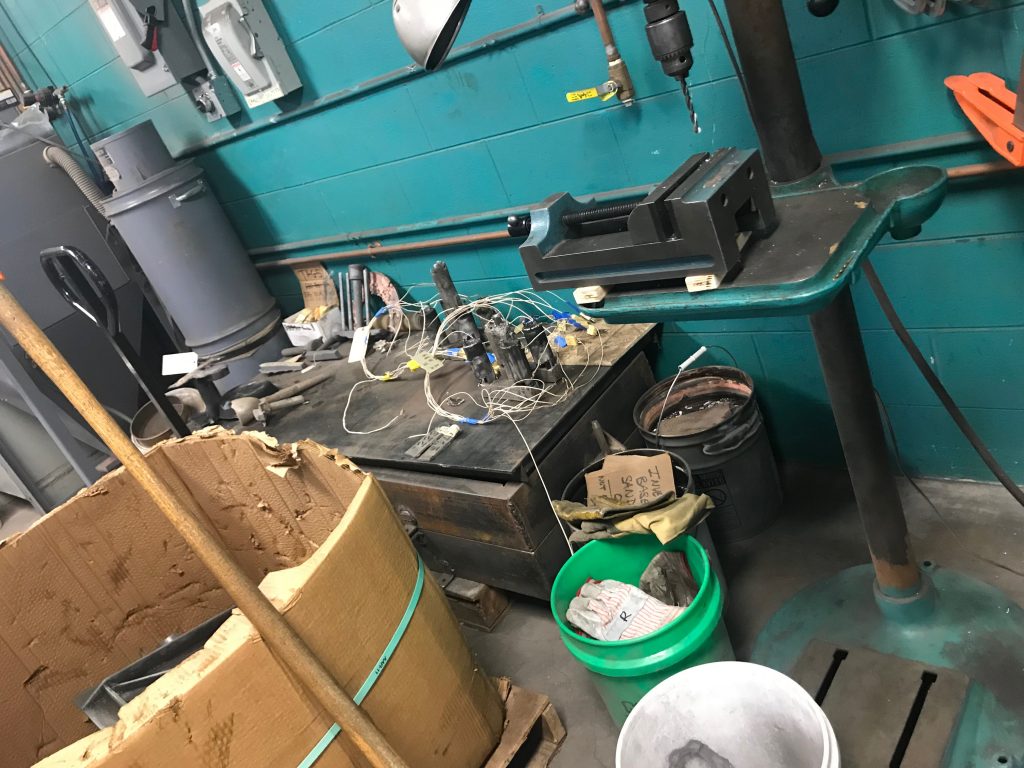
Now, these emotions I experienced weren’t necessarily circumstantial, however they’ve been encountered many times by many people and seem to be associated with any sort of change. Commonly, this sense of being overwhelmed is coupled with 5S. I’ve found that in most cases, when 5S is initiated, there’s usually a lot that needs to be done. These emotions can be used as a trigger to take a deep breath, and pick one incremental change at a time.